Robot compliance control method based on contact force observer
A technology of compliant control and contact force, applied in attitude control, three-dimensional position/channel control, etc., can solve problems such as low success rate, limited scope of application, poor adaptability, etc., and achieve the effect of reducing losses and saving development costs
- Summary
- Abstract
- Description
- Claims
- Application Information
AI Technical Summary
Problems solved by technology
Method used
Image
Examples
Embodiment Construction
[0026] Hereinafter, the present invention will be further described in detail with reference to the examples and drawings, but the embodiments of the present invention are not limited thereto. This specific embodiment selects a three-degree-of-freedom parallel robot (such as figure 2 Shown) as the target of action, but the implementation target is not limited to this, multi-degree-of-freedom tandem robots (such as image 3 (Shown) also applies.
[0027] The following will describe in detail the principle and implementation of the robot compliance control method based on the contact force observer of the present invention, so that those skilled in the art can understand the robot compliance control based on the contact force observer of the present invention without creative work. method.
[0028] Such as figure 1 As shown, the present invention provides a robot compliance control method based on a contact force observer specifically including the following steps:
[0029] step 1: ...
PUM
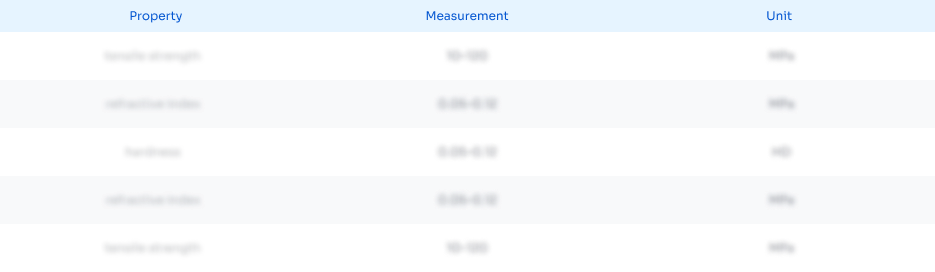
Abstract
Description
Claims
Application Information

- Generate Ideas
- Intellectual Property
- Life Sciences
- Materials
- Tech Scout
- Unparalleled Data Quality
- Higher Quality Content
- 60% Fewer Hallucinations
Browse by: Latest US Patents, China's latest patents, Technical Efficacy Thesaurus, Application Domain, Technology Topic, Popular Technical Reports.
© 2025 PatSnap. All rights reserved.Legal|Privacy policy|Modern Slavery Act Transparency Statement|Sitemap|About US| Contact US: help@patsnap.com