High-temperature mechanical sealing structure
A mechanical seal and high-temperature technology, which is applied to engine seals, mechanical equipment, engine components, etc., can solve the problems of difficult surface processing of ceramic materials, rising temperature of static ring and dynamic ring, and replacement of metal materials, etc., so as to improve the service life , reduce friction, good mechanical sealing performance
- Summary
- Abstract
- Description
- Claims
- Application Information
AI Technical Summary
Problems solved by technology
Method used
Image
Examples
Embodiment Construction
[0016] The present invention will be further described below in conjunction with the accompanying drawings and embodiments.
[0017] Such as figure 1 As shown, the static ring 4 of the present invention is coated with a layer of alloy coating 5, and the entire static ring is installed on the shaft, and the axis of the static ring is kept coincident with the axis of the shaft during installation. There are first set screws 3 on both sides of the outer symmetrical side of the sleeve 1, and the first set screws 3 pass through the sleeve 1 and connect to the outside of the static ring 4 and fix the static ring 4 in the axial direction to limit the rotation of the static ring 4, but The static ring 4 is allowed to move slightly along the axial direction. The end surface of the static ring 4 installed in the annular groove is connected to the bottom surface of the annular groove through the spring 2, and through the extrusion of the spring 2, the end surface of the static ring 4 ou...
PUM
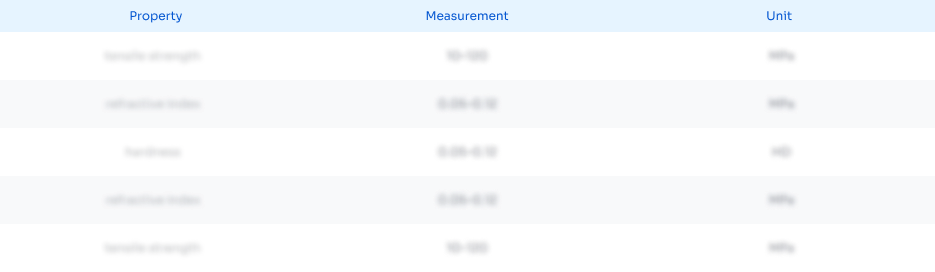
Abstract
Description
Claims
Application Information

- R&D Engineer
- R&D Manager
- IP Professional
- Industry Leading Data Capabilities
- Powerful AI technology
- Patent DNA Extraction
Browse by: Latest US Patents, China's latest patents, Technical Efficacy Thesaurus, Application Domain, Technology Topic, Popular Technical Reports.
© 2024 PatSnap. All rights reserved.Legal|Privacy policy|Modern Slavery Act Transparency Statement|Sitemap|About US| Contact US: help@patsnap.com