A Novel Fiber Bragg Grating Density Sensor Based on Differential Pressure Method
A density sensor, fiber grating technology, applied in instruments, scientific instruments, specific gravity measurement, etc., can solve the problems of few fiber grating sensors, low sensitivity of bare fiber grating sensors, and inability to meet engineering measurement accuracy, etc., to change detection sensitivity, reduce effect of influence
- Summary
- Abstract
- Description
- Claims
- Application Information
AI Technical Summary
Problems solved by technology
Method used
Image
Examples
Embodiment Construction
[0030] The present invention will be further described below in conjunction with the accompanying drawings and embodiments.
[0031] A novel fiber grating density sensor based on the differential pressure method such as figure 1 shown, including
[0032] Protective shell: a cylindrical shape, a first crossbeam is arranged along the diameter direction near the top, and a second crossbeam is arranged along the diameter direction near the bottom, the length of the first crossbeam and the second crossbeam are the same as the diameter, and they are parallel to each other;
[0033] The first corrugated diaphragm is fixed on the top of the protective shell along the horizontal plane, and the second corrugated diaphragm is fixed on the bottom of the protective shell along the horizontal plane; the two corrugated diaphragms are parallel to each other;
[0034] The first metal sensitization structure is fixed on the first beam and is in contact with the first corrugated diaphragm, and ...
PUM
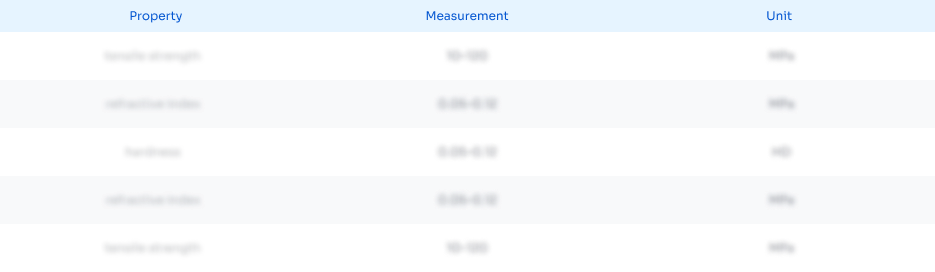
Abstract
Description
Claims
Application Information

- R&D Engineer
- R&D Manager
- IP Professional
- Industry Leading Data Capabilities
- Powerful AI technology
- Patent DNA Extraction
Browse by: Latest US Patents, China's latest patents, Technical Efficacy Thesaurus, Application Domain, Technology Topic, Popular Technical Reports.
© 2024 PatSnap. All rights reserved.Legal|Privacy policy|Modern Slavery Act Transparency Statement|Sitemap|About US| Contact US: help@patsnap.com