Control method for cabin door mechanism loading device
A control method and technology for loading equipment, which can be applied to controllers with specific characteristics, electric controllers, etc., can solve the problems of large speed conversion gradient and difficult control, and achieve feasible work, high reliability, and meet the requirements of loading performance. Effect
- Summary
- Abstract
- Description
- Claims
- Application Information
AI Technical Summary
Problems solved by technology
Method used
Examples
Embodiment Construction
[0013] A control method for the loading equipment of the hatch mechanism, which calculates the deviation e(k) of the hatch speed change according to the hatch motion state data collected by the system, and adjusts the PID parameters in a segmented control mode, wherein
[0014] When the deviation e(k)>E, take the control quantity u(k)=u(k-1)ΔU
[0015] Among them, E is a constant, indicating a threshold value for judging the movement state of the hatch, which is adjusted according to different working conditions. A negative number indicates that the direction of the movement state is opposite, and it is positive here in the opening and holding section. ΔU is a constant, expressing the electro-hydraulic servo in the loading actuator Valve control amount, where the opening holding section is positive; u(k) represents the control amount of the electro-hydraulic servo system valve;
[0016] When 0
[0017] Among them, fKP[e(k)] ref...
PUM
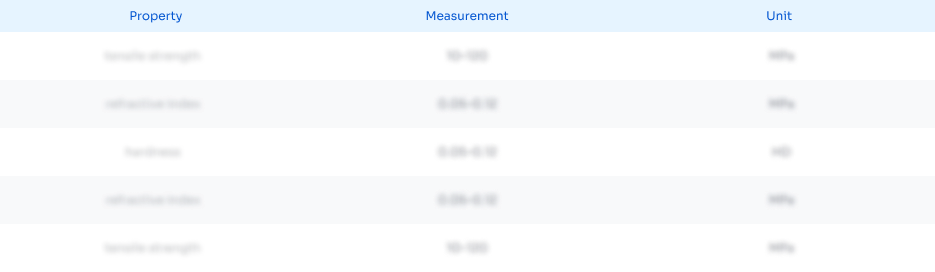
Abstract
Description
Claims
Application Information

- Generate Ideas
- Intellectual Property
- Life Sciences
- Materials
- Tech Scout
- Unparalleled Data Quality
- Higher Quality Content
- 60% Fewer Hallucinations
Browse by: Latest US Patents, China's latest patents, Technical Efficacy Thesaurus, Application Domain, Technology Topic, Popular Technical Reports.
© 2025 PatSnap. All rights reserved.Legal|Privacy policy|Modern Slavery Act Transparency Statement|Sitemap|About US| Contact US: help@patsnap.com