A Spinning Method for Revolving Curved Surface Parts with Front and Back Mounting Edges
A technology of rotating curved surface and parts, which is applied in the field of spinning and machining of rotating curved surface parts. It can solve the problems of unstable spinning elongation, inner sleeve spinning cracks, and large surface contour, so as to solve the problem of fracture, Effect of reducing extension resistance and improving surface quality
- Summary
- Abstract
- Description
- Claims
- Application Information
AI Technical Summary
Problems solved by technology
Method used
Image
Examples
Embodiment Construction
[0058] Below in conjunction with accompanying drawing and specific embodiment the present invention is described in further detail:
[0059]The specific steps of the spinning method of the rotary curved surface part with the front and rear mounting sides of the present invention are as follows:
[0060] First turn the forging to the pronation size, then spin the middle section, and then finish the non-spinning section.
[0061] Part spinning is a type of thinning spinning. According to the law of volume invariance, in order to ensure the shape and size of the parts after spinning, it is necessary to find out the changes in wall thickness reduction and shape, diameter and length of the spinning section, and then determine the shape and size of the blank before spinning.
[0062] like image 3 As shown, wall thickness reduction and spinning elongation.
[0063] Knowing the length of supination, thickness of the wall of supination, and radius of the arc of supination, and the ...
PUM
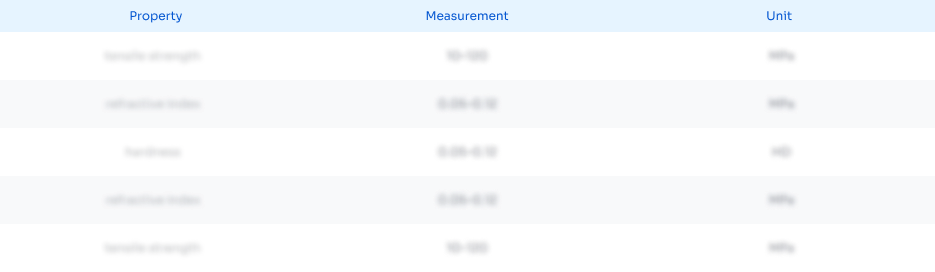
Abstract
Description
Claims
Application Information

- Generate Ideas
- Intellectual Property
- Life Sciences
- Materials
- Tech Scout
- Unparalleled Data Quality
- Higher Quality Content
- 60% Fewer Hallucinations
Browse by: Latest US Patents, China's latest patents, Technical Efficacy Thesaurus, Application Domain, Technology Topic, Popular Technical Reports.
© 2025 PatSnap. All rights reserved.Legal|Privacy policy|Modern Slavery Act Transparency Statement|Sitemap|About US| Contact US: help@patsnap.com