Headrest tube necking mould
A shrinking die and headrest tube technology, which is applied in metal processing equipment, forming tools, manufacturing tools, etc., can solve the problems of tube wall wrinkle damage, tube end shrinkage rate not greater than 25%, etc.
- Summary
- Abstract
- Description
- Claims
- Application Information
AI Technical Summary
Problems solved by technology
Method used
Image
Examples
Embodiment Construction
[0020] The present invention will be further described below in conjunction with the embodiments and accompanying drawings.
[0021] Such as figure 1 As shown, a headrest tube shrinking mold includes a mold body 1, and the mold body 1 is provided with a shrinking hole 2 communicating with the outside. The inner wall of the mouth hole 2 is a concave arc surface, and the diameter of the outer end of the necking hole 2 is d, and the inner wall of the necking hole 2 is divided into three sections of arc surfaces that are tangent to each other along the center line of the hole. The intersecting curve s can be obtained by intersecting any plane passing through the line direction with the inner wall of the necking hole 2, the arc radius of the outer section of the intersecting curve s is Ra, and the arc length is La; the arc radius of the middle section is Rb , the arc length is Lb; the arc radius of the inner section is Rc, the arc length is Lc, the inner end of the necking hole 2 ...
PUM
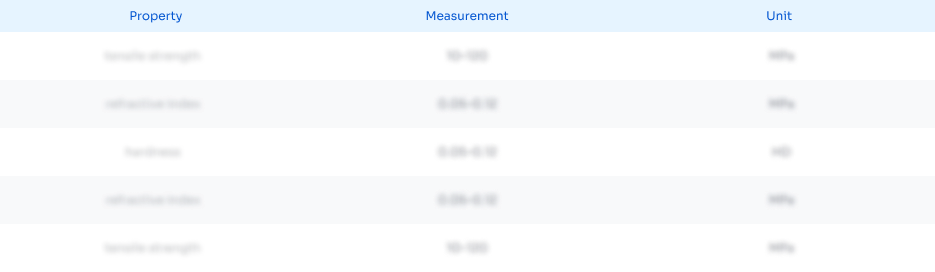
Abstract
Description
Claims
Application Information

- R&D Engineer
- R&D Manager
- IP Professional
- Industry Leading Data Capabilities
- Powerful AI technology
- Patent DNA Extraction
Browse by: Latest US Patents, China's latest patents, Technical Efficacy Thesaurus, Application Domain, Technology Topic, Popular Technical Reports.
© 2024 PatSnap. All rights reserved.Legal|Privacy policy|Modern Slavery Act Transparency Statement|Sitemap|About US| Contact US: help@patsnap.com