CAN bus connector of controller module
A CAN bus and controller module technology, applied in the field of automation control, can solve the problems of procurement, transportation, installation trouble, reliability reduction, complicated installation process, etc., to achieve the effect of reducing production and processing steps, reducing production links, and connecting firmly
- Summary
- Abstract
- Description
- Claims
- Application Information
AI Technical Summary
Problems solved by technology
Method used
Image
Examples
Embodiment Construction
[0022] The present invention will be described in further detail below in conjunction with the accompanying drawings and specific embodiments.
[0023] like figure 1 and image 3 As shown, a CAN bus connector of a controller module includes a housing 1, a module circuit board 2 is arranged inside the housing, and a male connector 3 and a female connector 3 are respectively connected to both sides of the module circuit board 2. Connector 4, the male connector 3 extends out of the housing 1, and the female connector 4 is located inside the housing 1. Those skilled in the art should understand that the end of the female connector 4 can be flush with the side of the housing 1, or It may be a recess and a side wall of the housing 1 . like Figure 4 As shown, the male connector 3 is compatible with the female connector 4 and when the two CAN bus connectors are close to each other, the male connector 3 on one CAN bus connector can be inserted into the female connector 4 on the oth...
PUM
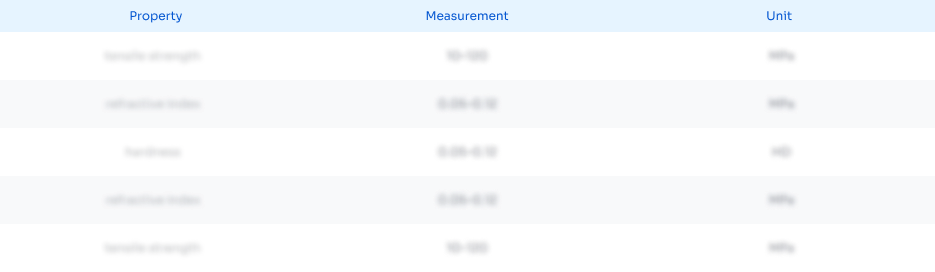
Abstract
Description
Claims
Application Information

- R&D
- Intellectual Property
- Life Sciences
- Materials
- Tech Scout
- Unparalleled Data Quality
- Higher Quality Content
- 60% Fewer Hallucinations
Browse by: Latest US Patents, China's latest patents, Technical Efficacy Thesaurus, Application Domain, Technology Topic, Popular Technical Reports.
© 2025 PatSnap. All rights reserved.Legal|Privacy policy|Modern Slavery Act Transparency Statement|Sitemap|About US| Contact US: help@patsnap.com