Master-slave robot control system and control method
A control system and control method technology, applied in the direction of program control of manipulators, manipulators, manufacturing tools, etc., can solve the problems of poor real-time performance, easy to generate multiple solutions, and many joints of hand robots, so as to reduce space following errors and avoid multiple Solubility and flexibility
- Summary
- Abstract
- Description
- Claims
- Application Information
AI Technical Summary
Problems solved by technology
Method used
Image
Examples
Embodiment Construction
[0030] In order to make the object, technical solution and advantages of the present invention clearer, the present invention will be further described in detail below in conjunction with the accompanying drawings and embodiments. It should be understood that the specific embodiments described here are only used to explain the present invention, not to limit the present invention.
[0031] see figure 1 , figure 1 It is a structural schematic diagram of the master-slave robot control system of the embodiment of the present invention. The master-slave robot control system of the embodiment of the present invention includes a master robot, a control system, an angle database and a slave robot. Among them, the slave robot includes an encoder. The control system is respectively connected with the main hand robot and the angle database, and the angle database is also connected with the slave hand robot. The control system receives the operation instructions of the master robot, ...
PUM
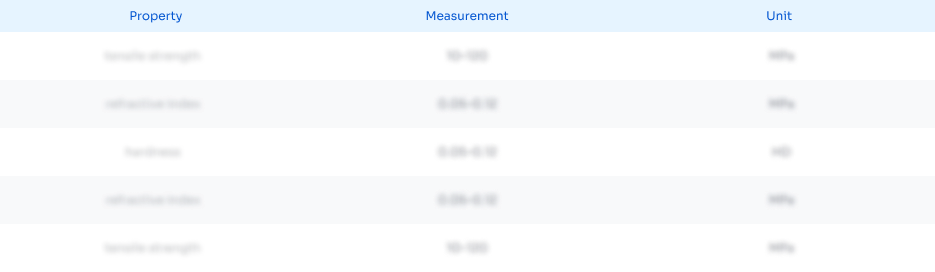
Abstract
Description
Claims
Application Information

- Generate Ideas
- Intellectual Property
- Life Sciences
- Materials
- Tech Scout
- Unparalleled Data Quality
- Higher Quality Content
- 60% Fewer Hallucinations
Browse by: Latest US Patents, China's latest patents, Technical Efficacy Thesaurus, Application Domain, Technology Topic, Popular Technical Reports.
© 2025 PatSnap. All rights reserved.Legal|Privacy policy|Modern Slavery Act Transparency Statement|Sitemap|About US| Contact US: help@patsnap.com