Resin-based powder metallurgy composite friction material for vehicle and preparation method thereof
A composite friction material, powder metallurgy technology, applied in the direction of friction linings, mechanical equipment, etc., can solve the problems of friction noise, scratches, etc., and achieve the effects of low wear toughness, good fit, and improved service life
- Summary
- Abstract
- Description
- Claims
- Application Information
AI Technical Summary
Problems solved by technology
Method used
Image
Examples
Embodiment 1
[0029] Preparation of short and fine iron-based powder metallurgy friction material: in terms of mass percentage, the basic formula of the material: iron 55%, tin 10%, quartz stone powder 10%, aluminum oxide 5%, molybdenum disulfide 5%; graphite powder 15% . The molding agent is kerosene, and the addition amount of the molding agent is 0.3% of the total weight of the basic formula of the above-mentioned materials. Mix the above materials evenly, pour them into the mold with a pressure of 500MPa, and press them into a slender rod shape with a diameter of φ2mm×200mm in length, separate each slender rod-shaped green compact, and put it into a sintering furnace. Under the conditions, the temperature rises to 1000°C, keeps the temperature for 4 hours, and cools to room temperature with the furnace.
[0030] Under dry conditions, it is placed for more than 24 hours; then it is cut, crushed, and screened with a 10-mesh sieve.
[0031] Preparation of composite friction material: bas...
Embodiment 2
[0037] Preparation of short and fine copper-based powder metallurgy friction material: basic material formula (by mass percentage): 60% copper, 5% nickel, 20% aluminum oxide, 5% molybdenum disulfide, and 10% graphite powder. The molding agent is kerosene, based on the total weight of the mixture, and the content of the molding agent is 0.5% by weight. Mix the above materials evenly, pour them into the mold with a pressure of 400MPa, and press them into a slender rod shape with a diameter of φ3mm×300mm in length, separate each slender rod-shaped green compact, and put it into a sintering furnace. Under the conditions, the temperature rises to 900°C, keeps the temperature for 5 hours, and cools down to room temperature with the furnace.
[0038] Under dry conditions, it is placed for more than 24 hours; then it is cut, crushed, and screened with an 8-mesh sieve.
[0039] Preparation of composite friction material: material basic formula (by mass percentage): cashew nut oil modi...
Embodiment 3
[0045] Preparation of short fine iron-based powder metallurgy friction material: basic material formula (by mass fraction): 65% iron, 2% tin, 10% quartz stone powder, 8% aluminum oxide, and 15% graphite powder. The forming agent is kerosene, based on the total weight of the mixture, and the content of the forming agent is 0.4% by weight. Mix the above materials evenly, pour them into the mold with a pressure of 500MPa, and press them into a slender rod shape with a diameter of φ3mm×300mm in length, separate each slender rod-shaped green compact, and put it into a sintering furnace. Under the conditions, the temperature rises to 1100°C, keeps warm for 2 hours, and cools down to room temperature with the furnace.
[0046] Under dry conditions, it is placed for more than 24 hours; then it is cut, crushed, and screened with an 8-mesh sieve.
[0047] Preparation of composite friction material: basic material formula (by mass percentage): cashew nut oil modified phenolic resin (She...
PUM
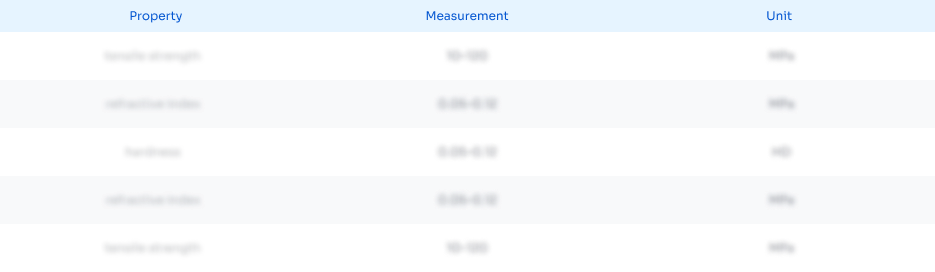
Abstract
Description
Claims
Application Information

- Generate Ideas
- Intellectual Property
- Life Sciences
- Materials
- Tech Scout
- Unparalleled Data Quality
- Higher Quality Content
- 60% Fewer Hallucinations
Browse by: Latest US Patents, China's latest patents, Technical Efficacy Thesaurus, Application Domain, Technology Topic, Popular Technical Reports.
© 2025 PatSnap. All rights reserved.Legal|Privacy policy|Modern Slavery Act Transparency Statement|Sitemap|About US| Contact US: help@patsnap.com