A friction stir welding laser calibration device and calibration method
A friction stir welding and calibrating device technology, which is applied in welding equipment, non-electric welding equipment, metal processing equipment, etc., can solve problems such as inability to achieve surface welding of complex workpieces, difficulty in ensuring consistency of weld strength, and complex shapes of areas to be welded , to achieve the effects of simple structure, improved welding quality and strong practicability
- Summary
- Abstract
- Description
- Claims
- Application Information
AI Technical Summary
Problems solved by technology
Method used
Image
Examples
Embodiment Construction
[0023] like Figure 1 to Figure 3 As shown, a friction stir welding laser calibration device of the present invention includes a camera 7, three prism bodies 9 and a convex lens 8, the camera 7 is located at the center of the main body support 2, and the camera 7 is fixed on the main body support 2 through the camera fixing plate 6 Above, the center of the convex lens 8 is provided with a through hole, the convex lens 8 is set on the camera fixed plate 6, there is a gap between the inner wall of the convex lens 8 and the camera fixed plate 6, the convex lens 8 is connected with the main body bracket 2 through the lens fixed plate 4, the convex lens 8 is installed on the main body support 2 through the base 5, the cover plate 1 is installed on the main body support 2, the base 5, the main body support 2 and the cover plate 1 are connected by bolts 3, and the three prism bodies 9 surround the center of the camera 7 The shaft circumference is evenly distributed, and the prism bod...
PUM
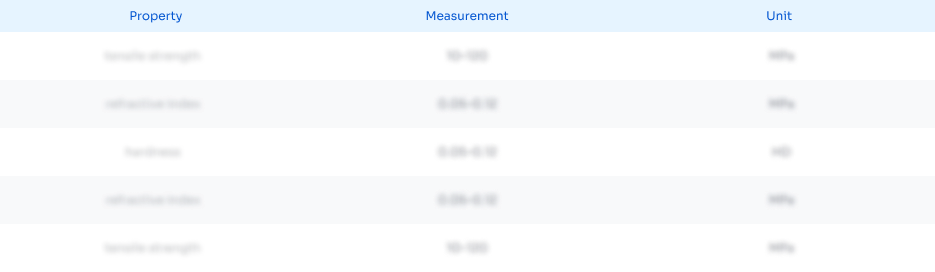
Abstract
Description
Claims
Application Information

- R&D Engineer
- R&D Manager
- IP Professional
- Industry Leading Data Capabilities
- Powerful AI technology
- Patent DNA Extraction
Browse by: Latest US Patents, China's latest patents, Technical Efficacy Thesaurus, Application Domain, Technology Topic, Popular Technical Reports.
© 2024 PatSnap. All rights reserved.Legal|Privacy policy|Modern Slavery Act Transparency Statement|Sitemap|About US| Contact US: help@patsnap.com