A train control system and test method for a test run line
A technology of train control system and test line, which is applied in the direction of operation center control system, vehicle route interaction equipment, transportation and packaging, etc. It can solve the problem of not equipped with effective CTCS-2/CTCS-3 level train control on-board equipment interface performance. Dynamic verification tests, etc.
- Summary
- Abstract
- Description
- Claims
- Application Information
AI Technical Summary
Problems solved by technology
Method used
Image
Examples
Embodiment 1
[0046] Such as figure 1 Shown is a frame diagram of a test line train control system provided by the present invention. The test line track of the system includes the first end track section, the first common braking section, the phase separation section, and the second common braking section. The section and the second end track section are sequentially connected to form, wherein, there is also a CTCS grade switching section between the phase-splitting section and the second common braking section, specifically:
[0047] The ground equipment of the system also includes a station train control center, track circuits, transponder groups, and line-side electronic equipment; the vehicle-mounted equipment includes an on-board host, wherein the on-board host includes a locomotive signal processor, a transponder signal receiving function, and a monitoring and recording device.
[0048] The track circuit is a circuit composed of rail lines and rail insulation, which is used to automa...
Embodiment 2
[0061] The embodiment of the present invention also provides a train control test method for a test run, based on the test train control test system described in Embodiment 1, when the specific test is a CTCS-2 test run, the method includes:
[0062] In step 201, the driver leads the car to the first track section at the end, and requests a test run to the station train control center;
[0063] In step 202, the station train control center returns a response, which carries the right to use the test run of the test run line;
[0064] In step 203, the driver starts the motor car and drives from the first end track section to the second end track section; after reaching the second end track section, the driver closes the driver's platform and starts again from the second end track section Start, change ends and travel to the first end track section;
[0065] In step 204, the test run ends, and the right to use the test run line is returned to the station interlocking system;
...
Embodiment 3
[0071] The embodiment of the present invention also provides a train control test method for a test run, based on the test train control test system described in Embodiment 1, the specific test is CTCS-3 level test run, the vehicle and the RBC simulation system establish a connection and a wireless communication session , the method includes:
[0072] In step 301, the driver leads the car to the first track section at the end, and requests a test run to the station train control center;
[0073] In step 302, the train control center of the station returns a response, which carries the right to use the test run of the test run line;
[0074] In step 303, the driver starts the motor car and drives from the first end track section to the second end track section; after reaching the second end track section, the driver closes the driver's platform and starts again from the second end track section Start, change ends and travel to the first end track section;
[0075] In step 304...
PUM
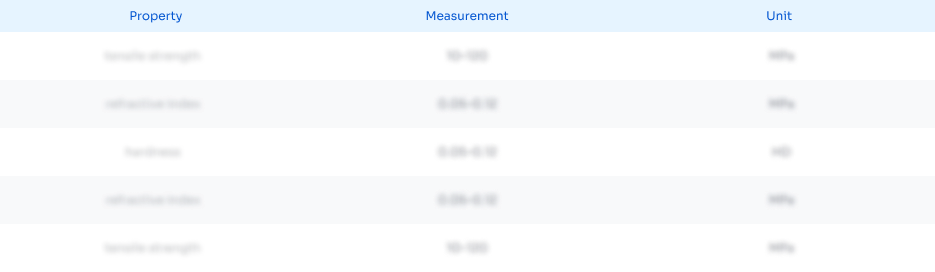
Abstract
Description
Claims
Application Information

- Generate Ideas
- Intellectual Property
- Life Sciences
- Materials
- Tech Scout
- Unparalleled Data Quality
- Higher Quality Content
- 60% Fewer Hallucinations
Browse by: Latest US Patents, China's latest patents, Technical Efficacy Thesaurus, Application Domain, Technology Topic, Popular Technical Reports.
© 2025 PatSnap. All rights reserved.Legal|Privacy policy|Modern Slavery Act Transparency Statement|Sitemap|About US| Contact US: help@patsnap.com