Structure of rope-driven mechanical arm rotation joint
A technology of rotating joints and mechanical arms, applied in the field of robotics, can solve the problems of multiple wheel sets, heavy weight, and complex mechanisms, and achieve the effect of easy protection and precise control
- Summary
- Abstract
- Description
- Claims
- Application Information
AI Technical Summary
Problems solved by technology
Method used
Image
Examples
Embodiment Construction
[0030] The specific implementation of the present invention will be further described in detail below in conjunction with the accompanying drawings, but the implementation of the present invention is not limited thereto.
[0031] Such as Figure 1 to Figure 4As shown, a structure of a rope-driven mechanical arm rotary joint includes a synchronous belt wheel shaft 1, a synchronous belt 8, an angle sensor 5, an arm joint bearing end cover 2, a deep groove ball bearing 6, an angular contact ball bearing 10, and a connection hole and the mechanical arm connecting the steel wire rope through hole, the synchronous pulley shaft 1 includes a pulley end 17 and a shaft end 19 from top to bottom, along the axis of the synchronous pulley shaft 1, a sensor accommodation hole 21, a sensor output Shaft connection hole 22, cross countersunk screw internal thread hole 23, the inner ring of the deep groove ball bearing 6 and the angular contact ball bearing 10 are respectively fixed on the uppe...
PUM
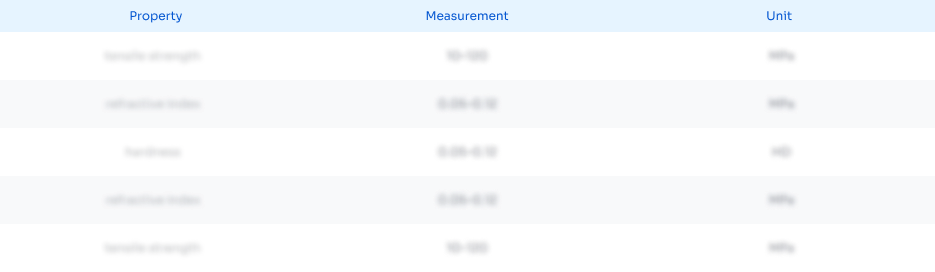
Abstract
Description
Claims
Application Information

- R&D
- Intellectual Property
- Life Sciences
- Materials
- Tech Scout
- Unparalleled Data Quality
- Higher Quality Content
- 60% Fewer Hallucinations
Browse by: Latest US Patents, China's latest patents, Technical Efficacy Thesaurus, Application Domain, Technology Topic, Popular Technical Reports.
© 2025 PatSnap. All rights reserved.Legal|Privacy policy|Modern Slavery Act Transparency Statement|Sitemap|About US| Contact US: help@patsnap.com