Filtrate reducer for drilling fluid and preparation method thereof
A technology of fluid loss reducer and drilling fluid, applied in chemical instruments and methods, drilling composition and other directions, can solve the problems of high temperature resistance and salt resistance of fluid loss reducer, and achieve good temperature resistance and salt resistance. Performance, good filtration effect
- Summary
- Abstract
- Description
- Claims
- Application Information
AI Technical Summary
Problems solved by technology
Method used
Image
Examples
preparation example Construction
[0029] The present invention also provides a kind of preparation method of drilling fluid fluid loss reducer, comprising the following steps:
[0030] Acrylamide, 2-acrylamide-2-methylpropanesulfonic acid, hexadecyl dimethyl allyl ammonium chloride, initiator and water are mixed and heated to obtain the fluid loss control agent for drilling fluid.
[0031] In the present invention, acrylamide, 2-acrylamide-2-methylpropanesulfonic acid, hexadecyl dimethyl allyl ammonium chloride, initiator and water are mixed. In the present invention, the method of mixing and heating is preferably carried out according to the following steps:
[0032] Mix acrylamide with water, stir to dissolve, then add 2-acrylamido-2-methylpropanesulfonic acid, stir to dissolve, then add hexadecyldimethylallyl ammonium chloride, stir to dissolve, and obtain mono Body mixed solution;
[0033] mixing and heating the monomer mixed solution with an initiator to obtain a gel product;
[0034] The gel product i...
Embodiment 1~9
[0066] According to the monomer ratio in Table 1, mix the acrylamide (AM) with water, stir to dissolve, then add 2-acrylamido-2-methylpropanesulfonic acid (AMPS), stir to dissolve, then add sixteen Alkyl dimethyl allyl ammonium chloride (DMAAC-16), stirring and dissolving, preparing a monomer mixed solution with a monomer concentration of 20 wt%, and adjusting the pH to 7 with sodium hydroxide solution;
[0067] The monomer mixed solution and the mass ratio are 1:1 (NH 4 ) 2 S 2 o 8 with NaHSO 3 The composite initiators were mixed and heated at 50° C. for 4 hours to obtain a gel product, wherein the added amount of the initiator accounted for 0.2 wt % of the total mass of the monomers.
[0068] The gel product was washed and purified three times with absolute ethanol, and the product was dried in an oven at a temperature of 50° C. for 24 hours to obtain a fluid loss reducer for drilling fluid.
[0069] Add 40g of calcium bentonite and 2g of anhydrous sodium carbonate to 1...
Embodiment 10~14
[0075] According to the molar ratio of AM, AMPS and DMAAC-16 is 2:4:0.5, mix the acrylamide (AM) with water, stir to dissolve, then add 2-acrylamido-2-methylpropanesulfonic acid (AMPS) , stirring and dissolving, then adding cetyl dimethyl allyl ammonium chloride (DMAAC-16), stirring and dissolving, preparing a monomer mixed solution with a monomer concentration of 20wt%, and adjusting the pH with sodium hydroxide solution = 7;
[0076] The monomer mixed solution and the mass ratio are 1:1 (NH 4 ) 2 S 2 o 8 with NaHSO 3 The composite initiators were mixed and heated at 50° C. for 4 hours to obtain a gel product, wherein the amount of the initiator added (relative to the total mass of the monomers) is shown in Table 2.
[0077] The gel product was washed and purified three times with absolute ethanol, and the product was dried in an oven at a temperature of 50° C. for 24 hours to obtain a fluid loss reducer for drilling fluid.
PUM
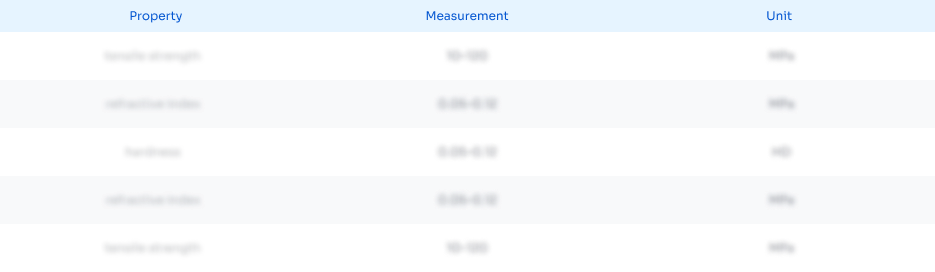
Abstract
Description
Claims
Application Information

- R&D
- Intellectual Property
- Life Sciences
- Materials
- Tech Scout
- Unparalleled Data Quality
- Higher Quality Content
- 60% Fewer Hallucinations
Browse by: Latest US Patents, China's latest patents, Technical Efficacy Thesaurus, Application Domain, Technology Topic, Popular Technical Reports.
© 2025 PatSnap. All rights reserved.Legal|Privacy policy|Modern Slavery Act Transparency Statement|Sitemap|About US| Contact US: help@patsnap.com