A full-scale aircraft structural test restraint system
A full-scale aircraft and structural testing technology, which is applied in the direction of aircraft component testing, etc., can solve the problems that affect the accuracy of test results and large deformation of landing gear, and achieve the effects of saving test costs, reducing impact, and simple structure
- Summary
- Abstract
- Description
- Claims
- Application Information
AI Technical Summary
Problems solved by technology
Method used
Image
Examples
Embodiment Construction
[0017] See attached Figures 1 to 2 , the full-scale aircraft structure test restraint system of the present invention is characterized in that, comprises restraint beam 2, top connection device 3, support lever 4, upward restraint device 5, upward restraint sensor 6, downward restraint device 7, downward restraint sensor 8 and ground fixed equipment 9.
[0018] When the restraint system of the aircraft structure test of the present invention is installed, the restraint beam 2 located above is connected with the support lever 4 through the top connecting device 3 to provide a fulcrum for the vertical restraint of the landing gear; one end of the support lever 4 passes through the upward restraint device 5 with an adjustable stroke It is connected with the ground fixed equipment 9, and the other end is connected with the upper end of the landing gear dummy wheel 1 through the upward restraint force sensor 6 to form a vertical upward constraint; the lower end of the landing gear...
PUM
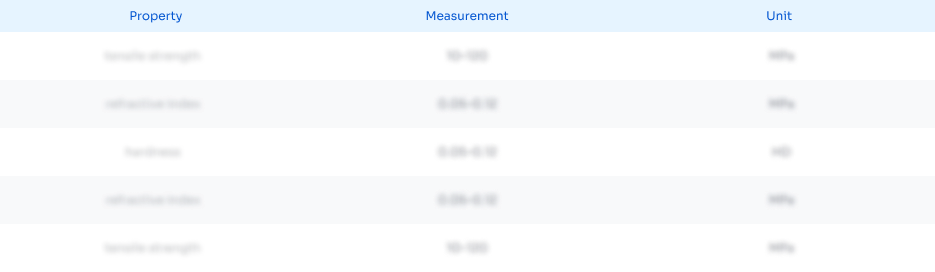
Abstract
Description
Claims
Application Information

- Generate Ideas
- Intellectual Property
- Life Sciences
- Materials
- Tech Scout
- Unparalleled Data Quality
- Higher Quality Content
- 60% Fewer Hallucinations
Browse by: Latest US Patents, China's latest patents, Technical Efficacy Thesaurus, Application Domain, Technology Topic, Popular Technical Reports.
© 2025 PatSnap. All rights reserved.Legal|Privacy policy|Modern Slavery Act Transparency Statement|Sitemap|About US| Contact US: help@patsnap.com