An attitude-changing valve assembly robot gripper and its working process
A technology of working process and robot hand, which is applied in the field of intelligent robots, can solve the problems of high cost, complicated process, and low efficiency, and achieve the effect of improving assembly efficiency, improving assembly accuracy, and reducing costs
- Summary
- Abstract
- Description
- Claims
- Application Information
AI Technical Summary
Problems solved by technology
Method used
Image
Examples
Embodiment 1
[0058] Such as figure 1 As shown, a valve assembly robot gripper that can change the attitude, including:
[0059] A fixing device, the fixing device is provided with a robot flange 11 for connecting the gripper with the robot;
[0060] Several guide rod cylinders 2 are fixedly arranged on the fixing device;
[0061] A plurality of single-hand claws are fixedly arranged on the fixing device, and are connected with the guide rod cylinder 2 in one-to-one correspondence, for grabbing the valve stem 01 .
[0062] Wherein, the single-hand claw can be a three-claw cylinder 31, which is connected to the guide rod cylinder 2 in one-to-one correspondence, and the different three-claw cylinders 31 are hinged to each other; in addition, the three-claw cylinder 31 is connected to the The fixture securely connects.
[0063] The three-claw cylinder 31 is provided with three claws 32, and the three-claw cylinder 31 is fixedly provided with the three claws 32 for grabbing the valve stem 01...
Embodiment 2
[0081] According to the posture-changing valve assembly robot gripper provided by the above-mentioned embodiments, this embodiment provides the working process of the valve assembly robot gripper capable of changing postures.
[0082] Such as Figure 7A As shown, the working process of a valve assembly robot gripper that can change the attitude includes the steps:
[0083] S1: All guide rod cylinders 2 shrink, and all single-hand claws open;
[0084] S2: Use the visual camera 4 to position the valve stem 01 to obtain the positioning information of the valve stem 01;
[0085] S3: The robot adjusts the position of the gripper according to the positioning information of the valve stem 01;
[0086] S4: All the guide rod cylinders 2 are stretched out, driving all the single-handed claws to gather together, so that the grasping directions of all the single-handed claws are consistent;
[0087] S5: Each of the single-hand claws grabs a valve stem 01 from the tray;
[0088] S6: us...
PUM
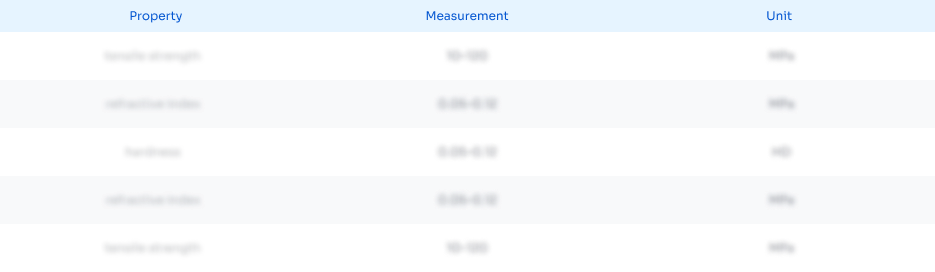
Abstract
Description
Claims
Application Information

- R&D Engineer
- R&D Manager
- IP Professional
- Industry Leading Data Capabilities
- Powerful AI technology
- Patent DNA Extraction
Browse by: Latest US Patents, China's latest patents, Technical Efficacy Thesaurus, Application Domain, Technology Topic, Popular Technical Reports.
© 2024 PatSnap. All rights reserved.Legal|Privacy policy|Modern Slavery Act Transparency Statement|Sitemap|About US| Contact US: help@patsnap.com