Pouring technology for castings
A casting and process technology, applied in the field of casting casting process, can solve the problems of complex casting process, low product market competitiveness, low production efficiency, etc. Effect
- Summary
- Abstract
- Description
- Claims
- Application Information
AI Technical Summary
Problems solved by technology
Method used
Examples
Embodiment Construction
[0008] The technical solution disclosed in the present invention is a casting pouring process, which is characterized in that it includes the following steps: 1) Preparatory work: (1) Check whether the ladle is dry and whether the sprue mouth is smooth and smooth before pouring every day, and the slag collecting agent Whether it is ready, whether the slag removal tool is ready, whether the products that need to add chilled iron are ready;
[0009] 2) Pouring: The first ladle of molten iron out of the furnace is used for pouring unimportant castings, and the waste castings are used instead of chilled iron. After each ladle of molten iron is poured, the slag collecting agent should be evenly sprinkled, and the slag removal machine should be used to remove the slag at the sprue. Clean, the height of the spout from the sprue cup is generally controlled between 150-200MM, the sprue cup should be kept full during pouring, and the pouring should not be interrupted under normal circums...
PUM
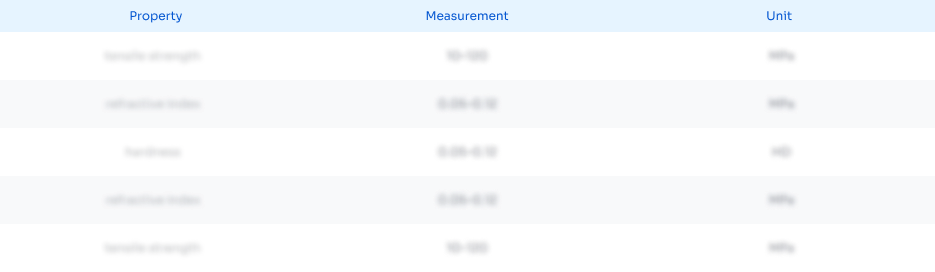
Abstract
Description
Claims
Application Information

- R&D
- Intellectual Property
- Life Sciences
- Materials
- Tech Scout
- Unparalleled Data Quality
- Higher Quality Content
- 60% Fewer Hallucinations
Browse by: Latest US Patents, China's latest patents, Technical Efficacy Thesaurus, Application Domain, Technology Topic, Popular Technical Reports.
© 2025 PatSnap. All rights reserved.Legal|Privacy policy|Modern Slavery Act Transparency Statement|Sitemap|About US| Contact US: help@patsnap.com