Process for taking down rusted broken stud screw with screw glue
A technology of screw and rust, applied in the field of rust and broken head screws, can solve the problems of taking out the screws that are not easy to break, the nut and the surfacing body are broken again, and the screw is broken.
- Summary
- Abstract
- Description
- Claims
- Application Information
AI Technical Summary
Problems solved by technology
Method used
Examples
Embodiment 1
[0020] Step 1: Use the lead punch to set the large positioning hole of the screw rod of the broken head screw. The diameter of the positioning hole is 1 / 2 of the diameter of the screw rod of the broken head screw;
[0021] Step 2: use the drill bit to drill the screw rod of the dead end screw from the positioning hole, the depth of the hole is 1.8 times of the screw diameter of the dead end screw, and the diameter of the hole is 1 / 2 of the screw diameter of the dead end screw;
[0022] Step 3: Use the welding rod to perform multiple surfacing welding from the inside of the hole to the outside of the hole until the surfacing body exposed by the surfacing welding is 6mm above the mechanical surface. The time of each surfacing welding is 3 seconds. After each surfacing welding, use metal The rod breaks up the welding slag, and then blows away the welding slag with a blower;
[0023] Step 4: Weld the nut on the surfacing body;
[0024] Step 5: Spray water on the screw rod of the ...
Embodiment 2
[0027] Step 1: Use the lead punch to set the large positioning hole of the screw rod of the broken head screw. The diameter of the positioning hole is 1 / 2 of the diameter of the screw rod of the broken head screw;
[0028] Step 2: use the drill bit to drill the screw rod of the dead end screw from the positioning hole, the depth of the hole is 2 times of the screw diameter of the dead end screw, and the diameter of the hole is 1 / 2 of the screw diameter of the dead end screw;
[0029] Step 3: Use the welding rod to perform multiple surfacing welding from the inside of the hole to the outside of the hole until the surfacing body exposed by 8mm of the mechanical surface. The time of each surfacing welding is 2 seconds. After each surfacing welding, use metal The rod breaks up the welding slag, and then blows away the welding slag with a blower;
[0030] Step 4: Weld the nut on the surfacing body;
[0031] Step 5: Spray water on the screw rod of the broken screw, the temperature ...
PUM
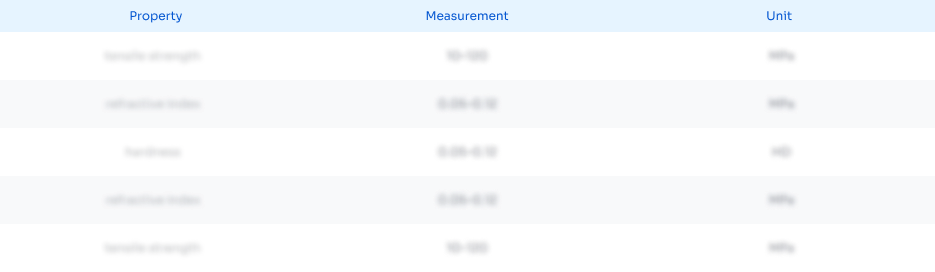
Abstract
Description
Claims
Application Information

- R&D
- Intellectual Property
- Life Sciences
- Materials
- Tech Scout
- Unparalleled Data Quality
- Higher Quality Content
- 60% Fewer Hallucinations
Browse by: Latest US Patents, China's latest patents, Technical Efficacy Thesaurus, Application Domain, Technology Topic, Popular Technical Reports.
© 2025 PatSnap. All rights reserved.Legal|Privacy policy|Modern Slavery Act Transparency Statement|Sitemap|About US| Contact US: help@patsnap.com