Serial flexible driving joint having steel wire transmission function
A joint and flexible technology, which is applied in the field of steel wire transmission series flexible drive joints, can solve the problems of series flexible drive joint structure redundancy, poor space adaptability, poor motion stability, etc. The effect of small loads
- Summary
- Abstract
- Description
- Claims
- Application Information
AI Technical Summary
Problems solved by technology
Method used
Image
Examples
specific Embodiment approach 1
[0015] Specific implementation mode one: combine Figure 1 to Figure 5 Describe this embodiment. This embodiment includes a support base plate 1, a joint drive assembly and an external support housing 15. The joint drive assembly includes a drive motor 2, a planetary reducer 3, a support flange 4, a reversing pinion bevel gear 5, and a transmission wire rope 7. Reversing large bevel gear 8, small sheave 9, large sheave 10, large sheave shaft 11, output piece 13, rope pretensioning device 14, two small sheave support bearings 6 and two large sheave shaft support bearings 12. The output part 13 is composed of an inverted U-shaped shift fork 13-1 and an output rod 13-2. The lower end of the inverted U-shaped wall of the inverted U-shaped shift fork 13-1 is provided with a mounting groove 13-1-1, and the output rod 13-1 2. Set on the inverted U-shaped shift fork 13-1, the output rod 13-2 is opposite to the inverted U-shaped wall on one side of the inverted U-shaped shift fork 13-1...
specific Embodiment approach 2
[0021] Specific implementation mode two: combination Figure 4 To illustrate this embodiment, the small sheave 9 of this embodiment is provided with a small sheave spiral groove 9-1, and the initial position and the end position of the small sheave spiral groove 9-1 are respectively provided with a transmission rope fixing hole 9-2 . Other components and connections are the same as those in the first embodiment.
specific Embodiment approach 3
[0022] Specific implementation mode three: combination Figure 5 The present embodiment is described. The large sheave 10 of the present embodiment is provided with a large sheave helical groove 10-2. Other components and connections are the same as those in the second embodiment.
PUM
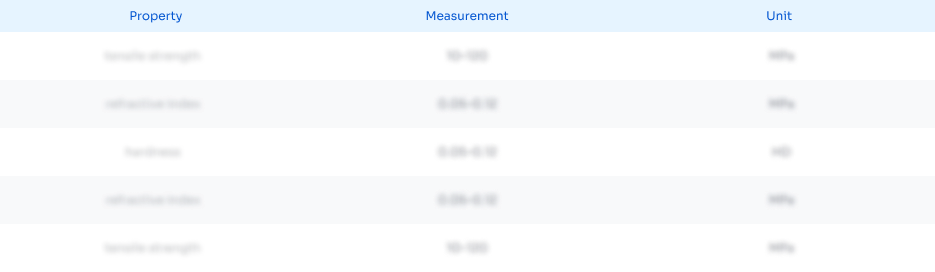
Abstract
Description
Claims
Application Information

- R&D Engineer
- R&D Manager
- IP Professional
- Industry Leading Data Capabilities
- Powerful AI technology
- Patent DNA Extraction
Browse by: Latest US Patents, China's latest patents, Technical Efficacy Thesaurus, Application Domain, Technology Topic, Popular Technical Reports.
© 2024 PatSnap. All rights reserved.Legal|Privacy policy|Modern Slavery Act Transparency Statement|Sitemap|About US| Contact US: help@patsnap.com