Polishing device and method for groove bottom
A technology of polishing device and polishing sheet, which is applied in the direction of grinding/polishing equipment, grinding/polishing hand tools, metal processing equipment, etc., can solve problems such as sealing strip falling off, surface flatness defects, etc., to reduce width difference, reduce The difference in surface flatness, the effect of reducing the probability of partial peeling
- Summary
- Abstract
- Description
- Claims
- Application Information
AI Technical Summary
Problems solved by technology
Method used
Image
Examples
Embodiment 1
[0038] refer to Figure 2 to Figure 4 , which shows a schematic diagram of an embodiment of the groove bottom polishing device of the present invention.
[0039] refer to figure 2 , The groove bottom polishing device provided in this embodiment includes: a cleaning head 20 , and a polishing sheet 21 mounted on the cleaning head 20 .
[0040] refer to image 3 , during the polishing process of the bottom 14 of the groove 13 on the back of the target backplate, the cleaning head 20 is embedded in the groove 13, and the polishing sheet 21 is attached to the bottom 14 of the groove 13 to clean the The bottom 14 of the groove 13 is polished to remove defects such as raised particles on the bottom 14 and improve the flatness of the bottom 14 of the groove 13 .
[0041] In this embodiment, the cleaning head 20 is a columnar structure, further optionally, the cleaning head 20 is a cylindrical structure, and the polishing sheet 21 is attached to the side wall of the cylindrical cle...
Embodiment 2
[0057] refer to Figure 5 and Figure 6 Shown is a schematic structural view of a groove bottom polishing device according to another embodiment of the present invention.
[0058] The similarities between the groove bottom polishing device in this embodiment and the groove bottom polishing device in Embodiment 1 will not be repeated, and the differences are:
[0059] In this embodiment, the cleaning head 40 is in the shape of a cubic column, and the polishing sheet 41 is attached to a side wall surface of the cubic column, and has a flat planar structure. Moreover, the width d5 of the polishing sheet 41 is smaller than the width of the bottom surface of the groove.
[0060] In this embodiment, the width d2 of the cleaning head 40 is larger than the width of the groove, so that after the cleaning head is embedded in the groove, the side wall of the cleaning head 40 is against the side wall of the groove to enhance polishing. Sheet 41 is positioned.
[0061] In this embodi...
PUM
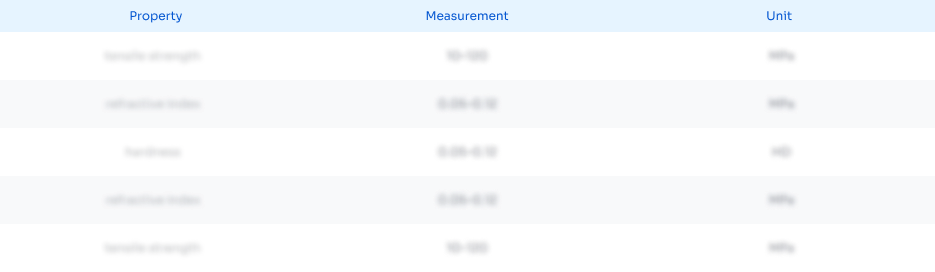
Abstract
Description
Claims
Application Information

- R&D
- Intellectual Property
- Life Sciences
- Materials
- Tech Scout
- Unparalleled Data Quality
- Higher Quality Content
- 60% Fewer Hallucinations
Browse by: Latest US Patents, China's latest patents, Technical Efficacy Thesaurus, Application Domain, Technology Topic, Popular Technical Reports.
© 2025 PatSnap. All rights reserved.Legal|Privacy policy|Modern Slavery Act Transparency Statement|Sitemap|About US| Contact US: help@patsnap.com