Turbine rear bearing case integrally connected with rectifying cascade
A load-bearing casing and rectifying cascade technology, applied in the field of aviation propulsion, to reduce weight, increase thrust-to-weight ratio, and shorten axial length
- Summary
- Abstract
- Description
- Claims
- Application Information
AI Technical Summary
Problems solved by technology
Method used
Image
Examples
Embodiment Construction
[0027] The present invention provides an integrated connection structure between the turbine rear bearing casing and the rectifying blade cascade. The present invention will be further described below in conjunction with the accompanying drawings and specific embodiments.
[0028] Such as figure 2 with image 3 As shown, in the integrated connection structure of the turbine rear bearing casing and the rectifying blade cascade according to an embodiment of the present invention, in addition to the rear bearing casing outer ring 2 included in the existing turbine rear bearing casing structure 1. In addition to the inner ring 9 of the rear load-bearing casing and the load-bearing support plate 11, the blades 4 are discretely installed between each load-bearing support plate 11 along the circumferential direction. The cascade structure includes the blade upper edge plate 3, the blade 4, Blade runner 5 and blade lower edge plate 6 .
[0029] Open threaded holes at the upper edge...
PUM
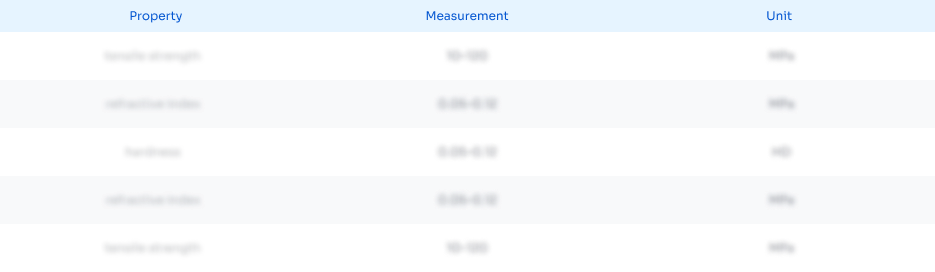
Abstract
Description
Claims
Application Information

- R&D Engineer
- R&D Manager
- IP Professional
- Industry Leading Data Capabilities
- Powerful AI technology
- Patent DNA Extraction
Browse by: Latest US Patents, China's latest patents, Technical Efficacy Thesaurus, Application Domain, Technology Topic, Popular Technical Reports.
© 2024 PatSnap. All rights reserved.Legal|Privacy policy|Modern Slavery Act Transparency Statement|Sitemap|About US| Contact US: help@patsnap.com