A pneumatic servo control system for high-altitude aircraft
A control system and aircraft technology, applied in general control systems, control/regulation systems, and electric fluid pressure control, etc., can solve the problems of slow response speed and unstable control, and reduce difficulty and false switching. Possibility, high precision and high response effect of real-time control
- Summary
- Abstract
- Description
- Claims
- Application Information
AI Technical Summary
Problems solved by technology
Method used
Image
Examples
Embodiment Construction
[0032] In order to make the object, technical solution and advantages of the present invention clearer, the present invention will be further described in detail below in conjunction with the accompanying drawings and embodiments. It should be understood that the specific embodiments described here are only used to explain the present invention, not to limit the present invention. In addition, the technical features involved in the various embodiments of the present invention described below can be combined with each other as long as they do not constitute a conflict with each other.
[0033]The invention provides an air pressure servo control system for high-altitude aircraft, which includes a positive pressure source, a controlled cavity, a control valve, a positive pressure source, a negative pressure source, a pressure sensor, a controller and a control valve. The chamber is a front-stage chamber and a rear-stage chamber. The pressure sensor includes a front-stage pressure...
PUM
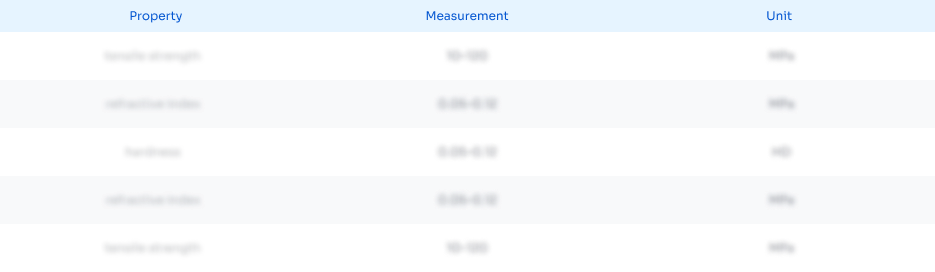
Abstract
Description
Claims
Application Information

- R&D
- Intellectual Property
- Life Sciences
- Materials
- Tech Scout
- Unparalleled Data Quality
- Higher Quality Content
- 60% Fewer Hallucinations
Browse by: Latest US Patents, China's latest patents, Technical Efficacy Thesaurus, Application Domain, Technology Topic, Popular Technical Reports.
© 2025 PatSnap. All rights reserved.Legal|Privacy policy|Modern Slavery Act Transparency Statement|Sitemap|About US| Contact US: help@patsnap.com