Closed pre-forging molding die for special-shaped oil spray device body workblank and process of closed pre-forging molding die
A technology of forming dies and fuel injectors, which is applied in the direction of manufacturing tools, metal processing equipment, forging/pressing/hammer devices, etc., can solve the problems of long original billet length, billet instability and wrinkling material utilization rate, etc., and achieve forging flow The effect of good line, easy mechanization and automation, and high material utilization rate
- Summary
- Abstract
- Description
- Claims
- Application Information
AI Technical Summary
Problems solved by technology
Method used
Image
Examples
Embodiment
[0022] Such as figure 1 As shown, a closed pre-forging mold for a special-shaped fuel injector body blank includes an upper mold base 4, a lower mold base 5, an upper mold 1 and a lower mold 2; the upper mold base 4 is provided with the same The upper mold 1 is matched with the through groove, and the upper mold 1 is fixedly arranged in the through groove. Specifically, the inner wall of the through groove is stepped, and the size of the upper end is larger than the size of the lower end. The upper mold 1 The upper end is provided with a protruding end 14 matching the size of the upper end of the through groove, and the upper die 1 and the upper die base 4 are fixed on the slider of the press through the protruding end 14 and the through groove; The lower mold base 5 is provided with a cavity matched with the lower mold 2, and the lower mold 2 is slidably arranged in the lower mold base 5 through the cavity, and the bottom of the cavity is in contact with the lower mold base ...
PUM
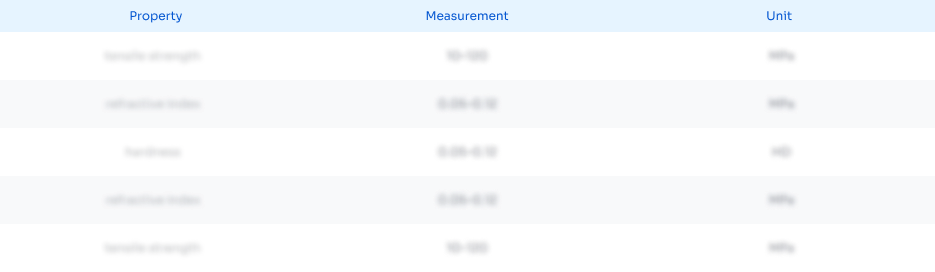
Abstract
Description
Claims
Application Information

- R&D
- Intellectual Property
- Life Sciences
- Materials
- Tech Scout
- Unparalleled Data Quality
- Higher Quality Content
- 60% Fewer Hallucinations
Browse by: Latest US Patents, China's latest patents, Technical Efficacy Thesaurus, Application Domain, Technology Topic, Popular Technical Reports.
© 2025 PatSnap. All rights reserved.Legal|Privacy policy|Modern Slavery Act Transparency Statement|Sitemap|About US| Contact US: help@patsnap.com