Blade dynamic frequency test apparatus using magnetic excitation
A technology of dynamic frequency and testing equipment, which is applied in vibration testing, measuring equipment, testing of machine/structural components, etc., can solve problems such as overheating of testing equipment, temperature rise, nitrogen pressure loss, etc., to improve equipment safety, Switching control is simple and the effect of increasing service time
- Summary
- Abstract
- Description
- Claims
- Application Information
AI Technical Summary
Problems solved by technology
Method used
Image
Examples
Embodiment Construction
[0039] The present invention will be described in further detail below in conjunction with the accompanying drawings.
[0040] see figure 1 , the present invention is a blade dynamic frequency test device using magnetic excitation, including a vacuum cylinder 6, and a front swing frame 3 and a rear swing frame 4 installed in the vacuum cylinder 6, the impeller 1 to be tested together with the rotating shaft 2 Installed on the front swing frame 3 and the rear swing frame 4, and fixed on the swing frame track 5 inside the vacuum cylinder 6, the front section of the rotating shaft 2 is connected with the output shaft of the drive motor 8 outside the vacuum cylinder 6 with a coupling 7 .
[0041] One or more magnetic exciters 15 can be selected to be arranged along the circumference of the impeller 1 , and the magnetic exciter bracket 16 is fixed on the rail 5 of the swing frame in the vacuum cylinder 6 . The receiving antenna 9 is fixed on the front swing frame 3 together with th...
PUM
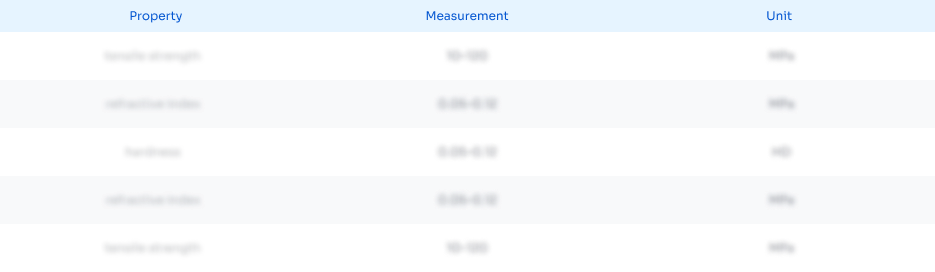
Abstract
Description
Claims
Application Information

- R&D
- Intellectual Property
- Life Sciences
- Materials
- Tech Scout
- Unparalleled Data Quality
- Higher Quality Content
- 60% Fewer Hallucinations
Browse by: Latest US Patents, China's latest patents, Technical Efficacy Thesaurus, Application Domain, Technology Topic, Popular Technical Reports.
© 2025 PatSnap. All rights reserved.Legal|Privacy policy|Modern Slavery Act Transparency Statement|Sitemap|About US| Contact US: help@patsnap.com