Operation method for socket pressing plate
An operation method and platen technology, applied in the field of molds, can solve the problems of difficulty in guaranteeing the precision of plastic products, and achieve the effects of simple structure, convenient operation and improved work efficiency.
- Summary
- Abstract
- Description
- Claims
- Application Information
AI Technical Summary
Problems solved by technology
Method used
Image
Examples
Embodiment 1
[0013] A long limit screw 3 is set on one side of the front template 1 and the rear template 2 so that the front template 1 and the rear template 2 are combined into one, and the extrusion gap 4 is formed between the front template 1 and the rear template 2, and the middle part of the front template 1 is positioned A gating system 6 is arranged under the middle part of the ring 5 and the positioning ring 5. The gating system 6 is in the shape of a "six", and a pair of molds 8 are symmetrically arranged on both sides of the middle part of the lower edge of the front formwork 1. The glue-out of the mold 8 and the gating system 6 Corresponding to the setting of the mouth, at least one nozzle needle 7 is set on both sides of the lower side of the positioning ring 5, and a core 9 is set corresponding to the mold 8 on both sides of the front of the rear template 2, and a push rod 10 is set inside the core 9, and the outer periphery of the core 9 After the internal thread 11, the fron...
Embodiment 2
[0015] Adjust the long limit screw 3 so that the front template 1 and the rear template 2 are merged together, the extrusion gap 4 between the front template 1 and the rear template 2 is 0.05-0.1mm, the pouring tube is fixed with the front template 1 through the positioning ring 5, The glue in the pouring tube enters the pouring system 6 from the pouring port and enters the cavity between the mold 8 and the core 9 from the glue outlet, and the cooling liquid in the nozzle needle 7 cools the pouring system 6 to keep the pouring system 6 at the setting Within the temperature range, the temperature of the glue when it enters from the gate is 110-120°C, the injection pressure is 90 Pa, and the time is 3 seconds. After entering the cavity, the temperature is 290°C, and the holding pressure is 65 Pa. The time is 2 seconds, the temperature of the second stage is 280°C, the temperature of the third stage is 269°C, and the temperature of the fourth stage is 250°C. The pressure-holding p...
PUM
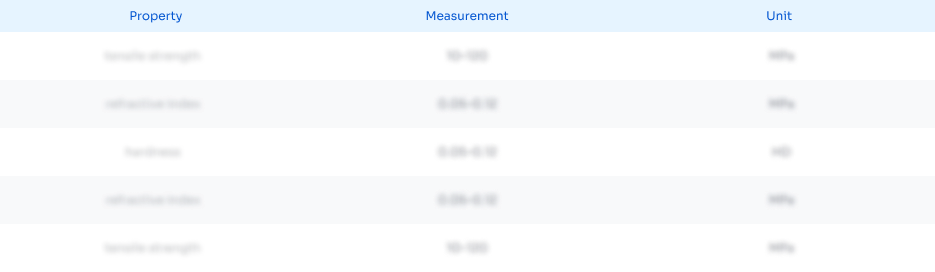
Abstract
Description
Claims
Application Information

- R&D Engineer
- R&D Manager
- IP Professional
- Industry Leading Data Capabilities
- Powerful AI technology
- Patent DNA Extraction
Browse by: Latest US Patents, China's latest patents, Technical Efficacy Thesaurus, Application Domain, Technology Topic, Popular Technical Reports.
© 2024 PatSnap. All rights reserved.Legal|Privacy policy|Modern Slavery Act Transparency Statement|Sitemap|About US| Contact US: help@patsnap.com