A kind of color-changing artificial leather and its preparation method
A technology of artificial leather and color-changing layer, which is applied in the field of artificial leather, can solve problems such as poor surface friction, and achieve the effects of easy operation, easy promotion, and improved wear resistance
- Summary
- Abstract
- Description
- Claims
- Application Information
AI Technical Summary
Problems solved by technology
Method used
Image
Examples
preparation example Construction
[0019] The present invention also provides a method for preparing the above-mentioned color-changing artificial leather. The preparation raw materials for the surface layer are mixed according to the above-mentioned ratio to form a surface layer slurry, and the surface layer slurry is coated on a release paper, and heated at 130-160° C. Dry under the same conditions for 60-70S; mix the raw materials for the preparation of the color-changing layer according to the above ratio to form a color-changing layer slurry, and then apply the color-changing layer slurry on the dried surface layer slurry at 150-170 Dry at ℃ for 70-80S; mix the preparation raw materials of the foam layer according to the above ratio to form a foam layer slurry, and then apply the foam layer slurry on the dried color-changing layer slurry, at 170 The foaming reaction is carried out at -190°C, and the time of the foaming reaction is 80-90 seconds, and then the polyurethane adhesive is coated on the foam layer...
Embodiment 1
[0028] A preparation method for color-changing artificial leather. Weigh and mix 100 parts by weight of polyurethane resin, 80 parts by weight of MEK and 1 part by weight of (A-375) peeling aid to form a surface layer slurry, and first set the coating gap, and then coat the surface layer slurry on the release paper, and dry it at 130°C for 60S; weigh 100 parts by weight of polyvinyl chloride resin, 80 parts by weight of dioctyl phthalate, bicarbonate 40 parts by weight of calcium, 1 part by weight of BaZn stabilizer and 3 parts by weight of PVC color paste are mixed together to form a color-changing layer slurry, and then the color-changing layer slurry is coated on the dried surface layer slurry On, dry at 150°C for 70S; weigh 100 parts by weight of polyvinyl chloride resin, 80 parts by weight of dioctyl phthalate, CaCO 3 60 parts by weight, 2 parts by weight of KZn stabilizer and 3 parts by weight of AC foaming agent are mixed together to form a foamed layer slurry, and then...
Embodiment 2
[0030] A preparation method for color-changing artificial leather. The surface layer raw materials of 100 parts by weight of polyurethane resin, 100 parts by weight of MEK and 3 parts by weight of (A-375) peeling aid are weighed and mixed to form a surface layer slurry. gap, and then coat the surface layer slurry on the release paper, and dry it at 160°C for 70S; weigh 100 parts by weight of polyvinyl chloride resin, 100 parts by weight of dioctyl phthalate, bicarbonate 60 parts by weight of calcium, 3 parts by weight of BaZn stabilizer and 5 parts by weight of PVC color paste are mixed together to form a color-changing layer slurry, and then the color-changing layer slurry is coated on the dried surface layer slurry On, dry at 170°C for 80S; weigh 100 parts by weight of polyvinyl chloride resin, 90 parts by weight of dioctyl phthalate, CaCO 370 parts by weight, 3 parts by weight of KZn stabilizer and 4 parts by weight of AC foaming agent are mixed together to form a foam laye...
PUM
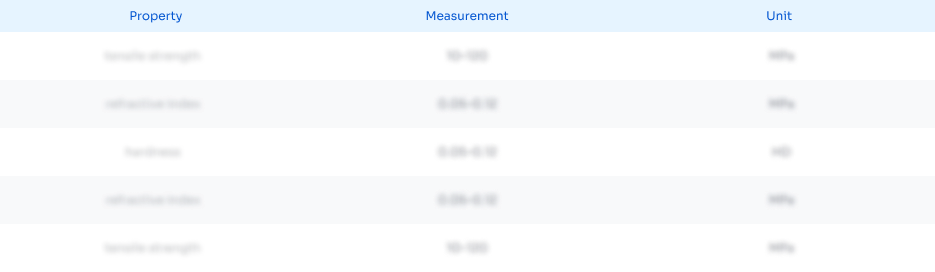
Abstract
Description
Claims
Application Information

- R&D
- Intellectual Property
- Life Sciences
- Materials
- Tech Scout
- Unparalleled Data Quality
- Higher Quality Content
- 60% Fewer Hallucinations
Browse by: Latest US Patents, China's latest patents, Technical Efficacy Thesaurus, Application Domain, Technology Topic, Popular Technical Reports.
© 2025 PatSnap. All rights reserved.Legal|Privacy policy|Modern Slavery Act Transparency Statement|Sitemap|About US| Contact US: help@patsnap.com