Production technology of carbon fiber composite aircraft
A composite material and production process technology, which is applied in the field of air pressure forming carbon fiber composite aircraft production technology, can solve the problems of inability to produce carbon fiber composite aircraft, and achieve high production efficiency and accurate processing dimensions
- Summary
- Abstract
- Description
- Claims
- Application Information
AI Technical Summary
Problems solved by technology
Method used
Image
Examples
Embodiment Construction
[0023] The present invention will be further described below in conjunction with the accompanying drawings and specific embodiments.
[0024] See figure 1 , a kind of carbon fiber composite material aircraft production process that the preferred embodiment of the present invention designs, comprises drawing confirmation, design latex airbag liner and EPS mandrel, mold design and manufacture, make latex airbag liner, material preparation, yarn cutting successively , preforming, forming, trimming and cutting, gluing, fine soil filling and coating process steps, the specific process steps are as follows:
[0025] Step 1, drawing confirmation. Carry out process analysis based on product drawings to evaluate whether each part of the product drawing is suitable for process production, such as fillet, size, strength and shape of each part, etc. If there are parts that are not suitable for process production, modify the product drawing.
[0026] Step 2, design the latex air bag line...
PUM
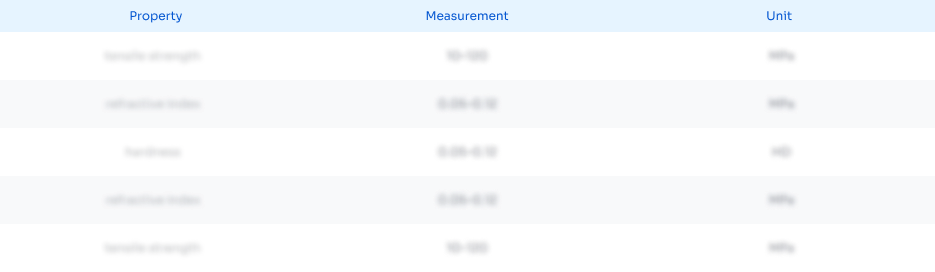
Abstract
Description
Claims
Application Information

- R&D Engineer
- R&D Manager
- IP Professional
- Industry Leading Data Capabilities
- Powerful AI technology
- Patent DNA Extraction
Browse by: Latest US Patents, China's latest patents, Technical Efficacy Thesaurus, Application Domain, Technology Topic, Popular Technical Reports.
© 2024 PatSnap. All rights reserved.Legal|Privacy policy|Modern Slavery Act Transparency Statement|Sitemap|About US| Contact US: help@patsnap.com