Fibre sensor assembly
An optical fiber sensor, optical fiber technology, applied in the field of bearings, can solve the problem of thermal damage of optical fiber sensors
- Summary
- Abstract
- Description
- Claims
- Application Information
AI Technical Summary
Problems solved by technology
Method used
Image
Examples
Embodiment Construction
[0026] figure 1 An axial cross-section of the bearing 1 is shown, comprising an inner bearing ring 2 with inner raceways 5 and an outer bearing ring 3 with outer raceways 6 . Rolling elements 4 are arranged between the inner and outer rings 2, 3 so that the inner and outer bearing rings 2, 3 can rotate relative to each other. The rolling elements 4 are located between the inner and outer raceways 5 , 6 .
[0027]The grooves 7 are provided on the outer surface 8 of the outer bearing ring 3 . The groove 7 accommodates a fiber optic sensor 9, which includes an optical fiber. In turn, the grooves 7 are provided with channels 12 . The channel 12 is shaped as a recess between the two side walls 10 which form an increase in the thickness of the outer bearing ring 3 .
[0028] The fiber optic sensor 9 is accommodated in the groove 7 and is connected to the outer bearing ring by means of a clamping ring 11 . The clamping ring 11 is accommodated in the channel 12 . The clamping ri...
PUM
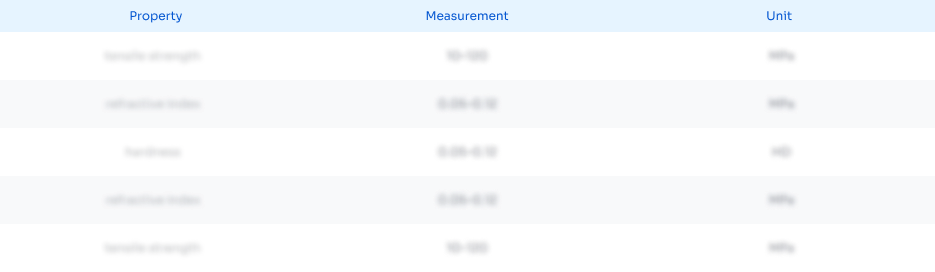
Abstract
Description
Claims
Application Information

- R&D
- Intellectual Property
- Life Sciences
- Materials
- Tech Scout
- Unparalleled Data Quality
- Higher Quality Content
- 60% Fewer Hallucinations
Browse by: Latest US Patents, China's latest patents, Technical Efficacy Thesaurus, Application Domain, Technology Topic, Popular Technical Reports.
© 2025 PatSnap. All rights reserved.Legal|Privacy policy|Modern Slavery Act Transparency Statement|Sitemap|About US| Contact US: help@patsnap.com