Multi-point synchronous hydraulic jacking system
A hydraulic, multi-point technology, applied in the direction of lifting devices, etc., can solve the problems of increasing project input cost, prolonging construction time, and slow lifting speed.
- Summary
- Abstract
- Description
- Claims
- Application Information
AI Technical Summary
Problems solved by technology
Method used
Image
Examples
Embodiment Construction
[0012] The present invention will be further described below in conjunction with specific examples.
[0013] In this embodiment, a general control box controls two sub-control boxes, and each sub-control box controls six jacks as an example for illustration.
[0014] A multi-point synchronous hydraulic jacking system. Twelve jacks 7 are evenly divided into two groups. Each jack 7 is equipped with a displacement sensor 8 for detecting its displacement. The oil inlet end of each jack 7 is connected to There is an electromagnetic valve 6, and the output ends of six displacement sensors 8 in each group are all connected with a sub-control box 3, and the output ends of the sub-control box 3 are respectively electrically connected with six electromagnetic valves 6 in the same group; The oil inlet end of the solenoid valve 6 is connected to the oil pump 4 through the main oil pipe; the speed limiting valve 5 is arranged on the main oil pipe between the oil pump 4 and the solenoid val...
PUM
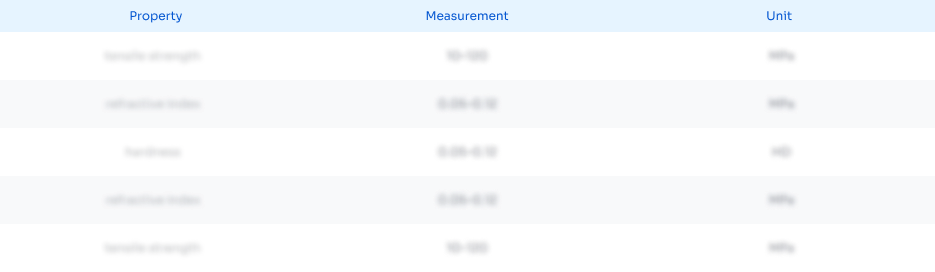
Abstract
Description
Claims
Application Information

- R&D Engineer
- R&D Manager
- IP Professional
- Industry Leading Data Capabilities
- Powerful AI technology
- Patent DNA Extraction
Browse by: Latest US Patents, China's latest patents, Technical Efficacy Thesaurus, Application Domain, Technology Topic, Popular Technical Reports.
© 2024 PatSnap. All rights reserved.Legal|Privacy policy|Modern Slavery Act Transparency Statement|Sitemap|About US| Contact US: help@patsnap.com