Large-diameter hemispherical fibrous composite winding method
A fiber composite material and large-diameter technology, which is applied in the field of material science, can solve the problems of large investment, low molding efficiency, and high cost, and achieve the effect of solving a large amount of calculation and reducing the workload
- Summary
- Abstract
- Description
- Claims
- Application Information
AI Technical Summary
Problems solved by technology
Method used
Image
Examples
specific Embodiment approach 1
[0015] Specific implementation mode one: combine Figure 1 to Figure 4 To illustrate this embodiment, a large-diameter hemispherical fiber composite material winding method described in this embodiment is realized through the following steps:
[0016] Step 1. Establish winding coordinate system:
[0017] Take the geometric center of the flat head 1-1 of mandrel 1 as the origin, take the axial direction of mandrel 1 as Y axis, take the radial direction of mandrel 1 as Z axis, and take the circumferential direction of mandrel 1 as X axis to establish XOYZ coordinate system;
[0018] Step 2, determine the winding track;
[0019] Step 3. Determine the trajectory of the wire winding nozzle;
[0020] Step 4. Calculating the movement coordinates of the winding nozzle, setting a number of control points on the hemispherical fiber winding trajectory, and calculating the movement coordinates of the winding nozzle in the hemispherical part respectively;
[0021] Step five, suturing t...
specific Embodiment approach 2
[0023] Specific implementation mode two: combination Figure 1 to Figure 4 Describe this embodiment, a large-diameter hemispherical fiber composite material winding method described in this embodiment, characterized in that: the specific steps for calculating the movement coordinates of the wire winding nozzle in step 4 are as follows:
[0024] Step 4 (1), input the original data, the original data includes the radius R of the hemisphere, the length L of the simple tube, and the distance S between the winding nozzle and the spherical surface t , barrel section winding angle α, advance amount B in sand width direction;
[0025] Step 4 (2), calculate the distance between the doffing point and the winding nozzle:
[0026] F = ( R + S t ) 2 ...
specific Embodiment approach 3
[0044] Specific implementation mode three: combination Figure 1 to Figure 4 Describe this embodiment, a large-diameter hemispherical fiber composite material winding method described in this embodiment, is characterized in that: in step 6, the specific steps for processing the core-to-mold winding ratio of the winding track are as follows:
[0045] Step six (1), calculate the winding speed ratio:
[0046] i 0 = Σ i = 0 i = n ( X i ) + Σ i = 0 i = ...
PUM
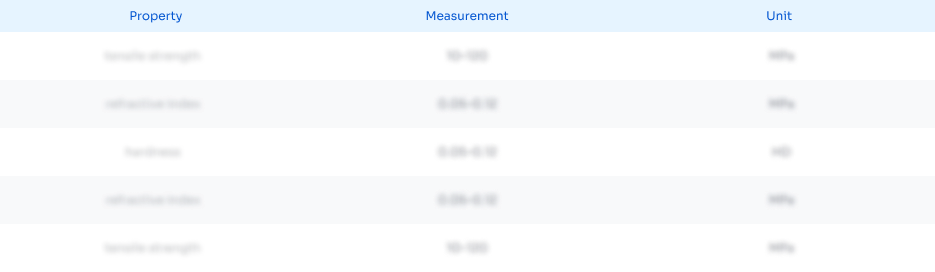
Abstract
Description
Claims
Application Information

- R&D Engineer
- R&D Manager
- IP Professional
- Industry Leading Data Capabilities
- Powerful AI technology
- Patent DNA Extraction
Browse by: Latest US Patents, China's latest patents, Technical Efficacy Thesaurus, Application Domain, Technology Topic, Popular Technical Reports.
© 2024 PatSnap. All rights reserved.Legal|Privacy policy|Modern Slavery Act Transparency Statement|Sitemap|About US| Contact US: help@patsnap.com