Casting defect repairing method
A technology for casting defects and castings, which is applied in the field of repairing casting defects, can solve problems such as unsatisfactory sealing, obvious traces on the repaired surface, and affecting the normal use of castings, etc., and achieves the effect of convenient operation
- Summary
- Abstract
- Description
- Claims
- Application Information
AI Technical Summary
Problems solved by technology
Method used
Image
Examples
Embodiment Construction
[0023] The specific implementation manners of the present invention will be described below in conjunction with the accompanying drawings.
[0024] combine figure 1 , figure 2 , image 3 , including the following steps:
[0025] a. According to the defect size of the casting, drill or tap the threaded bottom hole that can cover the casting defect, and bore a 10mm-15mm deep pin hole A on the upper part of the casting threaded bottom hole; the fitter grinds the lower end of the casting threaded bottom hole to form a 45° chamfer, for welding;
[0026] b. Making the plug: According to the thickness of the casting, make the upper part of the plug exposed to the rough part higher than the matching part of the pin C and the pin hole A, drill or tap the bottom of the plug to form the bottom thread, and process the lower end of the bottom thread of the plug to form a 45° cone angle. for welding;
[0027] c. Put the plug in liquid nitrogen and cool it for at least half an hour;...
PUM
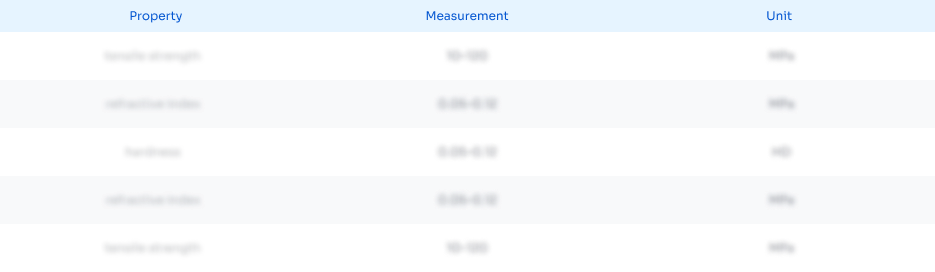
Abstract
Description
Claims
Application Information

- Generate Ideas
- Intellectual Property
- Life Sciences
- Materials
- Tech Scout
- Unparalleled Data Quality
- Higher Quality Content
- 60% Fewer Hallucinations
Browse by: Latest US Patents, China's latest patents, Technical Efficacy Thesaurus, Application Domain, Technology Topic, Popular Technical Reports.
© 2025 PatSnap. All rights reserved.Legal|Privacy policy|Modern Slavery Act Transparency Statement|Sitemap|About US| Contact US: help@patsnap.com