Fiber bragg grating sensor for measuring contact stress at rolling interface
A fiber grating and contact stress technology, which is applied in the field of strip rolling, can solve problems such as marks left by rolling strips, disturbance of friction conditions, and low stiffness of pressure measuring needles.
- Summary
- Abstract
- Description
- Claims
- Application Information
AI Technical Summary
Problems solved by technology
Method used
Image
Examples
Embodiment Construction
[0025] The following will clearly and completely describe the technical solutions in the embodiments of the present invention in combination with the embodiments of the present invention and the accompanying drawings. Obviously, the described embodiments are only some of the embodiments of the present invention, not all of them. Based on the embodiments of the present invention, all other embodiments obtained by persons of ordinary skill in the art without making creative efforts belong to the protection scope of the present invention.
[0026] see Figure 1-Figure 4 , in an embodiment of the present invention, a fiber grating sensor for measuring contact stress at a rolling interface, comprising a fiber grating rosette 1, a roll 2, a plug 3, a screw 4, an optical cable 5, a fiber collimator A6, and a collimator Fixed sleeve 7, fiber collimator B8, three-dimensional micro-displacement adjustment table 9. There is a stepped hole above the rolling area on the surface of the rol...
PUM
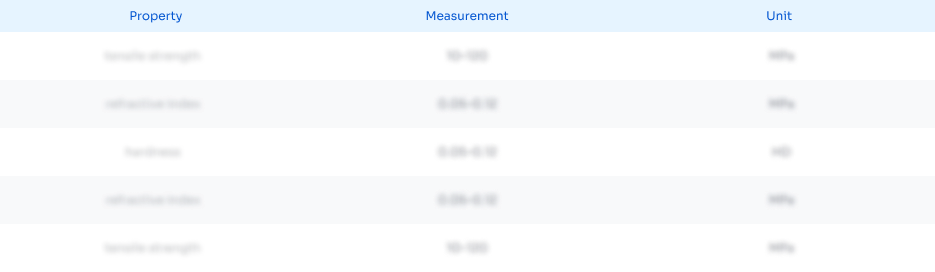
Abstract
Description
Claims
Application Information

- Generate Ideas
- Intellectual Property
- Life Sciences
- Materials
- Tech Scout
- Unparalleled Data Quality
- Higher Quality Content
- 60% Fewer Hallucinations
Browse by: Latest US Patents, China's latest patents, Technical Efficacy Thesaurus, Application Domain, Technology Topic, Popular Technical Reports.
© 2025 PatSnap. All rights reserved.Legal|Privacy policy|Modern Slavery Act Transparency Statement|Sitemap|About US| Contact US: help@patsnap.com