Ultrasonic flaw detection grading method for internal defects of steel ingot
A technology of internal defects and grading methods, which is applied in the analysis of solids using sonic/ultrasonic/infrasonic waves, which can solve the problems of inaccurate judgment, image, and intuition, and achieve the elimination of universal forging process cards, strong operability, and reasonable selection. Effect
- Summary
- Abstract
- Description
- Claims
- Application Information
AI Technical Summary
Problems solved by technology
Method used
Image
Examples
Embodiment 1
[0048]Example 1 The continuous casting ingot is tested, the material of the continuous casting billet is AISI 4130, and the size is Ф600×6000mm. Flaw detection is performed every 100mm from one end to the other. The surface of the steel ingot is polished at intervals of 0°, 45°, and 90°, and the width is about 100 mm, so that the surface roughness is 10 μm-30 μm, and the evaluation area is 100 mm×100 mm. Use the circumferential angles of A0, B45, and C90 to operate, and use A, B, and C as signs. The flaw detection sensitivity adopts the test block DAC method, adjusts the bottom wave to an appropriate height, then increases the ndB (eg: 18dB) as the flaw detection sensitivity, and records the equivalent result of flaw detection. The flaw detection equivalent of defect "A" angle is from -14 to -30dB; the flaw detection equivalent of "B" angle is from -13 to -30dB; the flaw detection equivalent of "C" angle is from -14 to -23dB. see Figure 15 , 16 and 17;
Embodiment 2
[0049] Example 2 The continuous casting ingot is tested, the material of the continuous casting billet is AISI 4130, and the size is Ф600×6000mm. Flaw detection is performed every 100mm from one end to the other. The surface of the steel ingot is ground at intervals of 0°, 120°, and 240°, with a width of about 100mm, so that the surface roughness is 10μm-30μm, and the evaluation area is 100mm×100mm. Use the circumferential angles of A0, B120, and C240 to operate, and use A, B, and C as signs. The flaw detection sensitivity adopts the test block DAC method, adjusts the bottom wave to an appropriate height, and then increases the ndB (eg: 18dB) as the flaw detection sensitivity, and records the grade division of flaw detection. The flaw detection grade of flaw "A" angle is from 1 to 3; the flaw detection grade of "B" angle is from 2 to 3; the flaw detection grade of "C" angle is from 2 to 3. see Figure 18 , 19 and 20 as shown;
Embodiment 3
[0050] Example 3 The continuous casting ingot is tested, the material of the continuous casting billet is AISI 4130, and the size is Ф600×6000mm. Flaw detection is performed every 100mm from one end to the other. The surface of the steel ingot is ground at intervals of 0°, 120°, and 240°, with a width of about 100mm, so that the surface roughness is 10μm-30μm, and the evaluation area is 100mm×100mm. Use the circumferential angle of A0 to operate, and use "A" as the logo. The flaw detection sensitivity adopts the test block DAC method, adjusts the bottom wave to an appropriate height, and then increases the ndB (eg: 18dB) as the flaw detection sensitivity, and records the grade division of flaw detection. Flaw "A" angles are graded from 0 to 4 for detection. The part of the shrinkage cavity defect in the center was sawed and analyzed at a low magnification. According to the analysis shown in the low magnification schematic diagram, there are concentrated holes in the local ce...
PUM
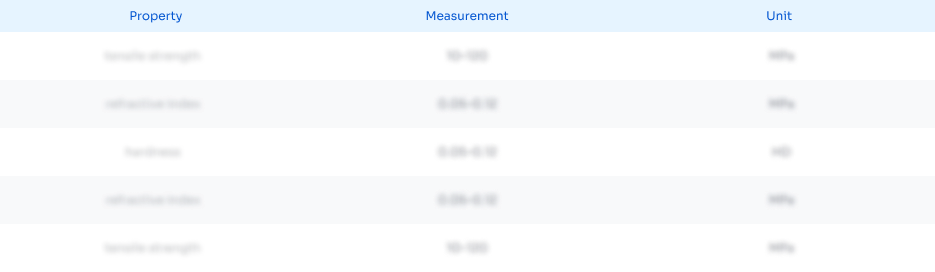
Abstract
Description
Claims
Application Information

- R&D
- Intellectual Property
- Life Sciences
- Materials
- Tech Scout
- Unparalleled Data Quality
- Higher Quality Content
- 60% Fewer Hallucinations
Browse by: Latest US Patents, China's latest patents, Technical Efficacy Thesaurus, Application Domain, Technology Topic, Popular Technical Reports.
© 2025 PatSnap. All rights reserved.Legal|Privacy policy|Modern Slavery Act Transparency Statement|Sitemap|About US| Contact US: help@patsnap.com