Non-hub motor balance switching drive for electric car
A technology for balanced drive and electric vehicles, applied in electric vehicles, control drives, vehicle components, etc., can solve the problems of limited maximum power of hubless motors, inability to reach the power of electric cars, and increased power consumption of gear transmission, so as to save Mechanical brakes, prevent tire blowouts, and improve the effect of anti-skid ability
- Summary
- Abstract
- Description
- Claims
- Application Information
AI Technical Summary
Problems solved by technology
Method used
Image
Examples
Embodiment Construction
[0024] figure 1 Middle (26)(28)(10) is connected to the positive pole of the battery in parallel, (29)(27)(11) is connected to the negative pole of the battery in parallel, pedal the Hall accelerator, (2) the red line input positive 5V, and the output signal line of the controller (30)(35)(5)(16) parallel output 5V connection, pedal Hall accelerator (1) green line (2) output signal and controller input signal line (31)(34)(6)(15 ) to connect the pedal Hall accelerator (4) black wire with (32) (33) (14) (7) controller negative electricity connection, controller (22) is connected with hubless motor (24), controller (17) and The hubless motor (20) is connected, the controller (19) is connected with the hubless motor (21), and the controller (23) is connected with the hubless motor (25).
[0025] Note: Description of drawings:
[0026] In specific implementation manners, the hubless motor controller is referred to as "controller" for short.
PUM
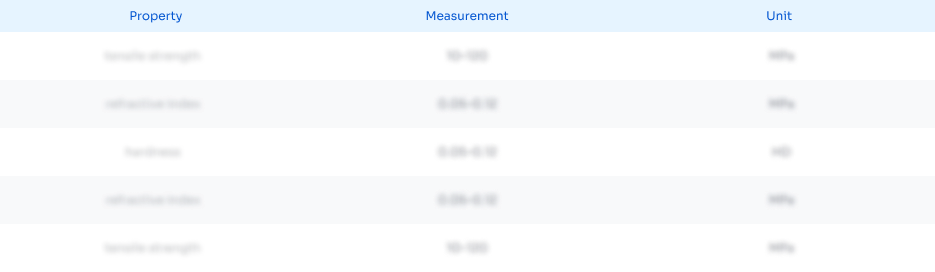
Abstract
Description
Claims
Application Information

- R&D
- Intellectual Property
- Life Sciences
- Materials
- Tech Scout
- Unparalleled Data Quality
- Higher Quality Content
- 60% Fewer Hallucinations
Browse by: Latest US Patents, China's latest patents, Technical Efficacy Thesaurus, Application Domain, Technology Topic, Popular Technical Reports.
© 2025 PatSnap. All rights reserved.Legal|Privacy policy|Modern Slavery Act Transparency Statement|Sitemap|About US| Contact US: help@patsnap.com