Partitioned paving molding die and method for multi-bundle and multi-positioning girder belts
A technology for forming molds and girder belts, which is applied in the field of composite material forming, can solve problems affecting the bearing effect of flexible beam girder belts, girder wrinkles, broken yarns and disordered yarns, and insufficient operating space, so as to achieve convenient implementation and avoid disordered yarns And the girder with wrinkles, the effect of ensuring quality
- Summary
- Abstract
- Description
- Claims
- Application Information
AI Technical Summary
Problems solved by technology
Method used
Image
Examples
Embodiment
[0022] Example: such as figure 1 , a composite material flexible beam composed of multi-beam number and multi-position girder strips. Such as Figure 5 , the piece is divided into pieces and pasted into forming tools. The structural characteristics of the lower mold body are: the symmetrical position of the front and rear edges of the flexible beam is used as the parting surface, and the lower mold body is divided into a main mold body and a movable block. The block can be moved 0-40mm away from the main mold body to give way to the laying space; a chute is set at the connection between the bottom of the movable block and the main mold body, so that the relative movement between the movable block and the main mold body follows a fixed track. The positioning pins of the two bushings at the inner and outer ends are respectively set on the two mold bodies, as the benchmark for the winding and positioning of the girder belt. The upper mold of the forming tooling is composed of t...
PUM
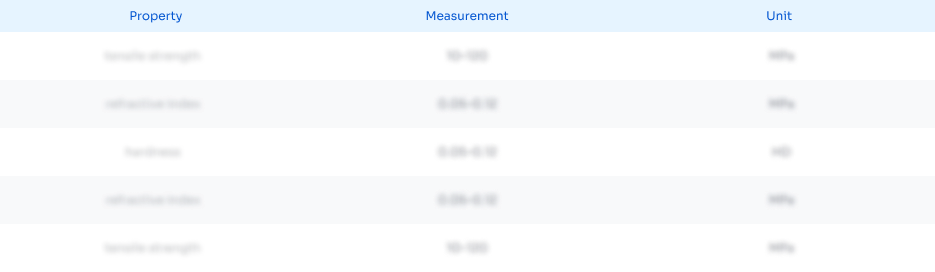
Abstract
Description
Claims
Application Information

- R&D
- Intellectual Property
- Life Sciences
- Materials
- Tech Scout
- Unparalleled Data Quality
- Higher Quality Content
- 60% Fewer Hallucinations
Browse by: Latest US Patents, China's latest patents, Technical Efficacy Thesaurus, Application Domain, Technology Topic, Popular Technical Reports.
© 2025 PatSnap. All rights reserved.Legal|Privacy policy|Modern Slavery Act Transparency Statement|Sitemap|About US| Contact US: help@patsnap.com