A loading and unloading mechanism
A guiding mechanism and driving motor technology, applied in the direction of conveyors, conveyor objects, mechanical conveyors, etc., can solve the problems of reducing the efficiency and reliability of AVG handling, high height, etc., to achieve large lifting range, save space, reduce The effect of small volume
- Summary
- Abstract
- Description
- Claims
- Application Information
AI Technical Summary
Problems solved by technology
Method used
Image
Examples
specific Embodiment approach
[0039] see figure 1 , figure 2 , Figure 6 and Figure 7 , a loading and unloading mechanism, including a mobile lifting mechanism 1, a guide mechanism and a roller conveying mechanism 4; A transmission mechanism; the guide track 202 is arranged on the inner side of the corresponding base 201, the two sides of the guide frame 203 are installed in the guide track 202, and the guide frame movable pulley 203A is respectively provided on the two sides of the guide frame 203, The movable pulley 203A of the guide frame can slide in the corresponding guide track 202 to facilitate the movement of the guide frame 203 . The drive motor 205 drives the guide frame 203 to slide, and the drive motor 205 is externally connected with a drive motor controller (not shown in the figure of the drive motor controller), which controls the forward rotation, reverse rotation and rotation of the drive motor 205. stop. An active channel 206 is provided between the bases 201; an RFID station card is...
PUM
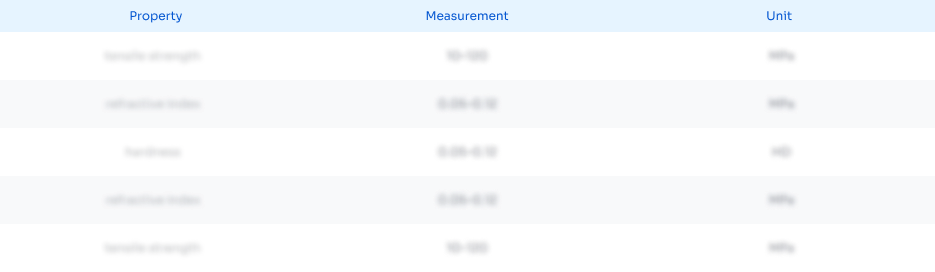
Abstract
Description
Claims
Application Information

- R&D
- Intellectual Property
- Life Sciences
- Materials
- Tech Scout
- Unparalleled Data Quality
- Higher Quality Content
- 60% Fewer Hallucinations
Browse by: Latest US Patents, China's latest patents, Technical Efficacy Thesaurus, Application Domain, Technology Topic, Popular Technical Reports.
© 2025 PatSnap. All rights reserved.Legal|Privacy policy|Modern Slavery Act Transparency Statement|Sitemap|About US| Contact US: help@patsnap.com