Thrust chamber injector of a hydrazine-based small-thrust single-component engine
A thrust chamber, small thrust technology, applied in machines/engines, rocket engine devices, mechanical equipment, etc., can solve problems such as poor craftsmanship, difficult processing, and difficult to determine flow characteristics.
- Summary
- Abstract
- Description
- Claims
- Application Information
AI Technical Summary
Problems solved by technology
Method used
Image
Examples
Embodiment Construction
[0014] The present invention is described in detail below in conjunction with accompanying drawing:
[0015] As shown in the figure, the injector of the present invention adopts a radial injection method to inject propellant radially from the thrust chamber. The structure of the injector includes an injection pipe 1, a thrust chamber 3, and an injection disk 2 , wherein the injection pipe 1 is fixed on the injection plate 2 and installed at the front end of the thrust chamber 3. In order to change the injection direction, a thrust chamber head baffle 4 is added at the front end of the thrust chamber to seal the front end of the thrust chamber. The injection plate 2 described above is an end cover structure that can envelop the front section of the thrust chamber, and is machined by bar material. The injection plate 2 shown in the figure is composed of two parts butt welding of the end cover and the connecting ring 5, which simplifies the processing technology. During processin...
PUM
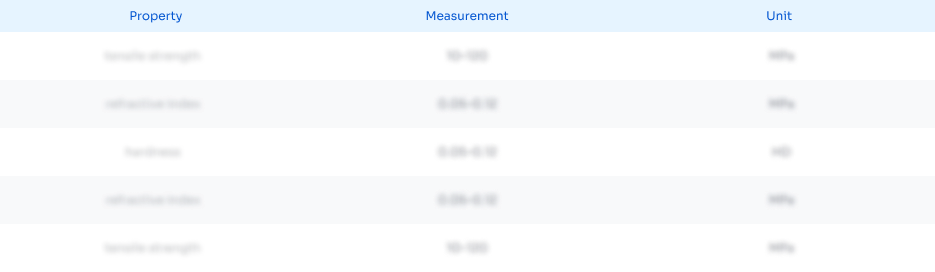
Abstract
Description
Claims
Application Information

- R&D Engineer
- R&D Manager
- IP Professional
- Industry Leading Data Capabilities
- Powerful AI technology
- Patent DNA Extraction
Browse by: Latest US Patents, China's latest patents, Technical Efficacy Thesaurus, Application Domain, Technology Topic.
© 2024 PatSnap. All rights reserved.Legal|Privacy policy|Modern Slavery Act Transparency Statement|Sitemap