Gypsum whisker dry method transformation method
A gypsum whisker and transformation technology, applied in the field of gypsum whisker dry transformation technology, can solve the problems of uneven crystal shape, low production efficiency, high production cost, etc.
- Summary
- Abstract
- Description
- Claims
- Application Information
AI Technical Summary
Problems solved by technology
Method used
Image
Examples
Embodiment 1
[0010] As shown in the figure, the lower end cover 5 of the autoclaved drying kettle 1 is sealed, and the gypsum whiskers are packed into the autoclaved drying kettle 1, preferably without the steam heat exchanger 2;
[0011] Seal the upper end cover 4 of the autoclaved steaming kettle 1, close the pressure relief port 9 on the kettle body and the drain port 6 of the lower end cover, and slightly open the exhaust port 7;
[0012] Simultaneously open the switch 13 and the switch 14 leading to the steam heat exchanger and the direct steam inlet on the steam sub-cylinder 3, and feed in steam at 130°C;
[0013] When the temperature displayed by the thermometer 10 in the autoclave 1 reaches 60° C., turn off the switch 14;
[0014] When the temperature displayed by the temperature gauge 10 in the autoclave 1 reaches 120°C and the pressure displayed by the pressure gauge 11 reaches 0.2MPa-0.5MPa, the switch 13 is turned off;
[0015] After heat preservation and pressure holding for ...
Embodiment 2
[0019] As shown in the figure, the lower end cover 5 of the autoclave 1 is sealed, and the gypsum whiskers are put into the autoclave 1, preferably to cover the steam heat exchanger 2;
[0020] Seal the upper end cover 4 of the autoclaved steaming kettle 1, close the pressure relief port 9 on the kettle body and the drain port 6 of the lower end cover, and slightly open the exhaust port 7;
[0021] Simultaneously open the switch 13 and the switch 14 leading to the steam heat exchanger and the direct steam inlet on the steam sub-cylinder 3, and feed steam at 150°C;
[0022] When the temperature displayed by the temperature gauge 10 in the autoclave 1 reaches 80°C-90°C, turn off the switch 14;
[0023] When the temperature displayed by the temperature gauge 10 in the autoclave 1 reaches 120°C-150°C, and the pressure displayed by the pressure gauge 11 reaches 0.2MPa-0.3MPa, the switch 13 is turned off;
[0024] After heat preservation and pressure holding for 3-6 hours, open the...
Embodiment 3
[0028] As shown in the figure, the lower end cover 5 of the autoclave 1 is sealed, and the gypsum whiskers are packed into the autoclave 1, preferably without the steam heat exchanger 2;
[0029] Seal the upper end cover 4 of the autoclaved steaming kettle 1, close the pressure relief port 9 on the kettle body and the drain port 6 of the lower end cover, and slightly open the exhaust port 7;
[0030] Simultaneously open the switch 13 and the switch 14 leading to the steam heat exchanger and the direct steam inlet on the steam sub-cylinder 3, and feed in steam at 190°C;
[0031] When the temperature displayed by the temperature gauge 10 in the autoclave 1 reaches 100° C., turn off the switch 14;
[0032] When the temperature displayed by the temperature gauge 10 in the autoclave 1 reaches 150°C and the pressure displayed by the pressure gauge 11 reaches 0.3MPa-0.5MPa, the switch 13 is turned off;
[0033] After heat preservation and pressure holding for 3-6 hours, open the pre...
PUM
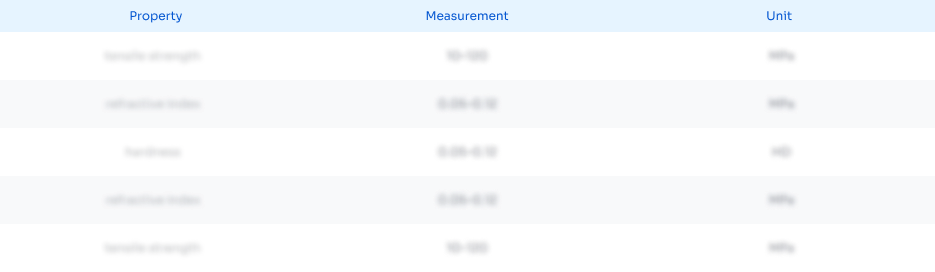
Abstract
Description
Claims
Application Information

- R&D
- Intellectual Property
- Life Sciences
- Materials
- Tech Scout
- Unparalleled Data Quality
- Higher Quality Content
- 60% Fewer Hallucinations
Browse by: Latest US Patents, China's latest patents, Technical Efficacy Thesaurus, Application Domain, Technology Topic, Popular Technical Reports.
© 2025 PatSnap. All rights reserved.Legal|Privacy policy|Modern Slavery Act Transparency Statement|Sitemap|About US| Contact US: help@patsnap.com