Wire winding machine with automatic cutter
A wire winding machine, automatic technology, applied in the direction of conveying filamentous materials, thin material processing, transportation and packaging, etc., can solve the problem of low winding efficiency
- Summary
- Abstract
- Description
- Claims
- Application Information
AI Technical Summary
Problems solved by technology
Method used
Image
Examples
Embodiment Construction
[0013] A multifunctional surface treatment wire winding machine, such as figure 1 As shown, it includes a revolving shaft 2 driven by a motor 1, and a signal control mechanism is provided on the side of the revolving shaft 2. device 5, a control module is connected to the signal end of the infrared transmitter 4 and the infrared receiver 5, and the distance from the infrared ray emitted by the infrared transmitter 4 to the infrared receiver 5 to the outer wall of the shaft 2 It is equal to the melt-blown thickness of the plastic wire of the wire-wound filter core rod.
[0014] A crimping shaft 3 for compacting plastic wire is arranged below the rotating shaft 2 , and both ends of the crimping shaft 3 are arranged on a slope 6 . The crimping shaft 3 presses and slides on the slope 6 as the thread on the rotating shaft 2 thickens.
[0015] The winding machine also includes a wire winding device, which includes a transmission mechanism arranged below the winding shaft 2 and a w...
PUM
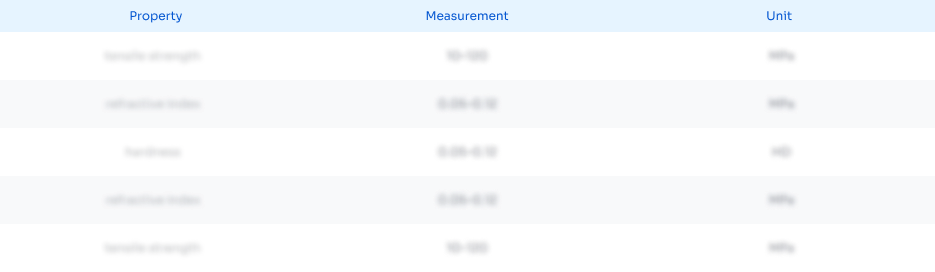
Abstract
Description
Claims
Application Information

- R&D Engineer
- R&D Manager
- IP Professional
- Industry Leading Data Capabilities
- Powerful AI technology
- Patent DNA Extraction
Browse by: Latest US Patents, China's latest patents, Technical Efficacy Thesaurus, Application Domain, Technology Topic, Popular Technical Reports.
© 2024 PatSnap. All rights reserved.Legal|Privacy policy|Modern Slavery Act Transparency Statement|Sitemap|About US| Contact US: help@patsnap.com