Method for calibrating sector sections of slab continuous casting machine online
A technology of slab continuous casting and calibration method, which is applied in the field of continuous casting machine roll gap calibration, can solve the problems of long time and low precision, and achieve the effect of improving operation rate, improving control precision and uniform force
- Summary
- Abstract
- Description
- Claims
- Application Information
AI Technical Summary
Problems solved by technology
Method used
Image
Examples
Embodiment 1
[0025] (1) Use spacers to level the two pairs of hydraulic cylinders on the inlet and outlet sides of each sector respectively.
[0026] (2) Press down the upper frame of the segment, and the force of the segment is required to be 800 kN.
[0027] (3) The mechanical engineer uses a hand-held roll gap meter to measure the left and right roll gaps of the segment head rolls, and the left and right roll gaps of the end rolls. Table 1 shows the actual measured roll gap value during calibration.
[0028] Table 1 Actual measurement of roll gap during sector calibration
[0029]
[0030] (4) Use the measured roll gap value to assign a value to the displacement sensor in the hydraulic cylinder of the segment, that is, to complete the calibration of the segment.
[0031] Casting number: 201207241512, steel type: Q345R slab specification: 300mm×1800mm, casting speed 0.85m / min. The low magnification rating of this poured slab sample is center segregation C1.5.
Embodiment 2
[0033] (1) Use spacers to level the two pairs of hydraulic cylinders on the inlet and outlet sides of each sector respectively.
[0034] (2) Press down the upper frame of the sector, requiring the force of the sector to be 2400 kN.
[0035] (3) The mechanical engineer uses a hand-held roll gap meter to measure the left and right roll gaps of the segment head rolls, and the left and right roll gaps of the end rolls. Table 2 shows the actual measured roll gap value during calibration.
[0036] Table 2 Actual measurement of roll gap during sector calibration
[0037]
[0038] (4) Use the measured roll gap value to assign a value to the displacement sensor in the hydraulic cylinder of the segment, that is, to complete the calibration of the segment.
[0039] Casting number: 201208241512, steel type: Q345D slab specification: 300mm×1800mm, casting speed 0.85 m / min. The low magnification rating of this cast slab sample is center segregation C0.5.
Embodiment 3
[0041] (1) Use spacers to level the two pairs of hydraulic cylinders on the inlet and outlet sides of each sector respectively. This work should be done before the calibration of the sector, and appropriate adjustments should be made as needed during the calibration.
[0042] (2) Press down the upper frame of the sector, requiring the force of the sector to be 4000 kN.
[0043] (3) The mechanical engineer uses a hand-held roll gap meter to measure the left and right roll gaps of the segment head rolls, and the left and right roll gaps of the end rolls. Table 3 shows the actual measured roll gap value during calibration.
[0044] Table 3 Actual measurement of roll gap during sector calibration
[0045]
[0046] (4) Use the measured roll gap value to assign a value to the displacement sensor in the hydraulic cylinder of the segment, that is, to complete the calibration of the segment.
[0047] Casting number: 201208301515, steel type: Q345D slab specification: 300mm×2400mm...
PUM
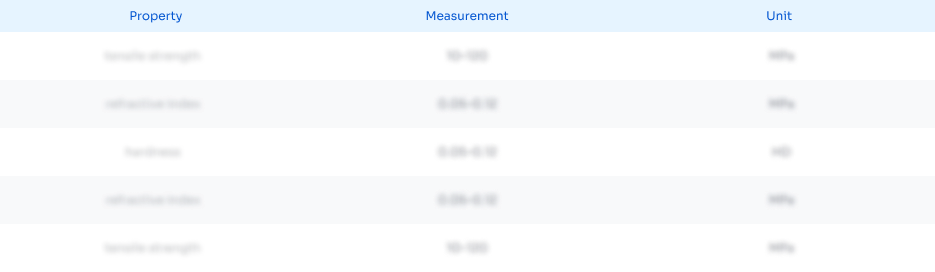
Abstract
Description
Claims
Application Information

- Generate Ideas
- Intellectual Property
- Life Sciences
- Materials
- Tech Scout
- Unparalleled Data Quality
- Higher Quality Content
- 60% Fewer Hallucinations
Browse by: Latest US Patents, China's latest patents, Technical Efficacy Thesaurus, Application Domain, Technology Topic, Popular Technical Reports.
© 2025 PatSnap. All rights reserved.Legal|Privacy policy|Modern Slavery Act Transparency Statement|Sitemap|About US| Contact US: help@patsnap.com