Automatic sand feeding apparatus
An automatic sand filling and sand storage technology, which is applied in metal processing equipment, casting molding equipment, cleaning/processing machinery of casting mold materials, etc., can solve the problems of fast sand dropping, loose sand, and high labor intensity, and achieve Convenient control, uniform sand discharge, and improved production efficiency
- Summary
- Abstract
- Description
- Claims
- Application Information
AI Technical Summary
Problems solved by technology
Method used
Image
Examples
Embodiment Construction
[0017] The technical solution will be described in detail below through a best embodiment, but the protection scope of the present invention is not limited to the embodiment.
[0018] refer to figure 1 As shown, an automatic sand adding device includes a sand storage box 1, a feeding port 3 and a mold sand box 10, and a quicksand chute 2 is arranged at the lower end of the sand storage box 1.
[0019] refer to figure 1 and figure 2 As shown, the discharge port 3 is arranged on the side of the sand storage box 1 close to the mold sand box 10 . The lower end of the discharge port 3 is provided with a conveying pipeline 5, and a sand inlet is arranged on the conveying pipe 5 to connect with the discharge port 3, and the discharge port 3 and the conveying pipe 5 are connected by a plane ring. A helical blade 7 is arranged in the conveying pipe 5 .
[0020] refer to figure 1 As shown, the delivery pipe 5 is provided with a drive motor 6 at one end close to the plane ring.
...
PUM
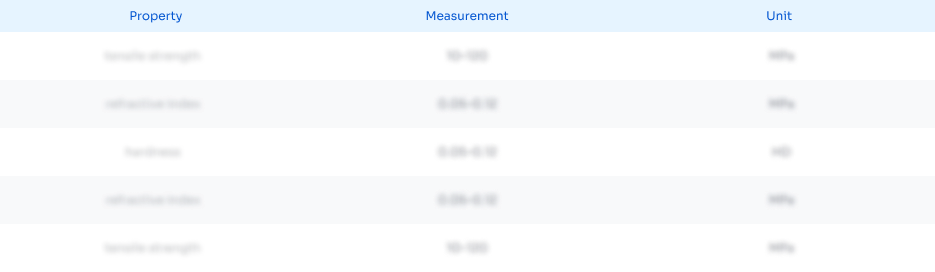
Abstract
Description
Claims
Application Information

- R&D Engineer
- R&D Manager
- IP Professional
- Industry Leading Data Capabilities
- Powerful AI technology
- Patent DNA Extraction
Browse by: Latest US Patents, China's latest patents, Technical Efficacy Thesaurus, Application Domain, Technology Topic, Popular Technical Reports.
© 2024 PatSnap. All rights reserved.Legal|Privacy policy|Modern Slavery Act Transparency Statement|Sitemap|About US| Contact US: help@patsnap.com