Automatic steering engine of low-speed wind tunnel force test model
A force measurement test and autopilot technology, applied in aerodynamic test, machine/structural component test, measurement device, etc., can solve the problems of high labor intensity, low test efficiency, affecting data quality, etc., so as to improve the use efficiency , easy to operate effect
- Summary
- Abstract
- Description
- Claims
- Application Information
AI Technical Summary
Problems solved by technology
Method used
Image
Examples
Embodiment Construction
[0026] All the features disclosed in this specification, or all disclosed methods or steps in the process, except for mutually exclusive features and / or steps, can be combined in any manner.
[0027] The automatic steering gear of the present invention is mainly composed of two parts, one is a mechanical transmission mechanism, and the other is a control system.
[0028] The thickness of the model airfoil in a low-speed wind tunnel of the order of 3 meters is relatively small, and the airfoil thickness near the control surface axis is generally 3-25mm, which determines that the angle control mechanism adopted is smaller in the thickness direction of the control surface. In addition, the control surface bears a certain aerodynamic load, so the output torque of the mechanism is required to be large enough to overcome the torque brought by the aerodynamic force. The transmission mechanism is small in size, high in processing accuracy, large in output torque, and difficult in design an...
PUM
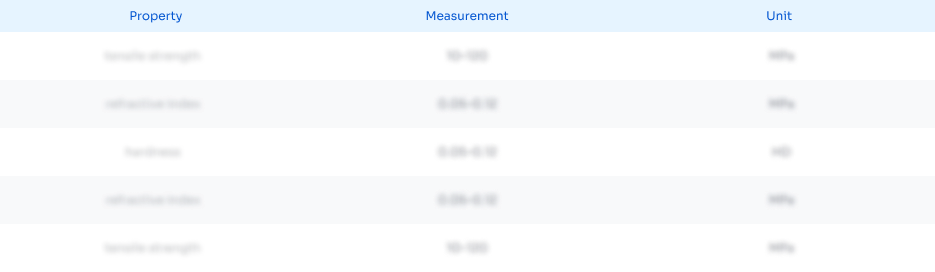
Abstract
Description
Claims
Application Information

- R&D
- Intellectual Property
- Life Sciences
- Materials
- Tech Scout
- Unparalleled Data Quality
- Higher Quality Content
- 60% Fewer Hallucinations
Browse by: Latest US Patents, China's latest patents, Technical Efficacy Thesaurus, Application Domain, Technology Topic, Popular Technical Reports.
© 2025 PatSnap. All rights reserved.Legal|Privacy policy|Modern Slavery Act Transparency Statement|Sitemap|About US| Contact US: help@patsnap.com