Torsional oscillation damping device
A technology of torsional vibration and attenuation devices, which is applied in transmission devices, rotation vibration suppression, fluid transmission devices, etc., can solve the problems of reduced vibration attenuation performance, failure to obtain vibration attenuation performance, increased man-hours or manufacturing costs, etc., to achieve vibration suppression and abnormal noise effects
- Summary
- Abstract
- Description
- Claims
- Application Information
AI Technical Summary
Problems solved by technology
Method used
Image
Examples
Embodiment Construction
[0026] Next, this invention is demonstrated more concretely. figure 1 It is a partially enlarged view showing an example of the torsional vibration damping device 1 according to the present invention, and schematically illustrates the centrifugal force acting on the mass body 3 mounted so as to be able to swing relative to the rotating body 2 , and the force toward the circumferential direction of the rotating body 2 does not act on the mass body 3 . The rotating body 2 is, for example, a disk-shaped member, and is configured to rotate integrally with a rotating shaft such as an output shaft of an engine or an input shaft of a transmission, not shown. exist figure 1 In the illustrated example, a pair of first hollow portions 4R, 4L are formed on the outer peripheral side of the rotating body 2 at a predetermined interval in the circumferential direction. Each of the first hollow portions 4R, 4L is formed in a hollow cylindrical shape as an example. The center of curvature o...
PUM
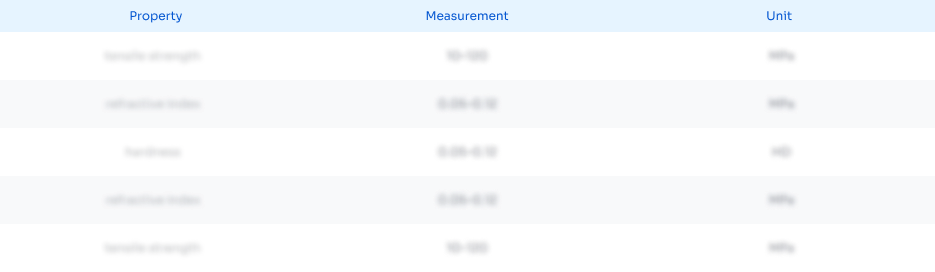
Abstract
Description
Claims
Application Information

- R&D
- Intellectual Property
- Life Sciences
- Materials
- Tech Scout
- Unparalleled Data Quality
- Higher Quality Content
- 60% Fewer Hallucinations
Browse by: Latest US Patents, China's latest patents, Technical Efficacy Thesaurus, Application Domain, Technology Topic, Popular Technical Reports.
© 2025 PatSnap. All rights reserved.Legal|Privacy policy|Modern Slavery Act Transparency Statement|Sitemap|About US| Contact US: help@patsnap.com