A method for obtaining the position angle of the motor rotor
A technology of motor rotor and position angle, which is applied in the direction of electronic commutator, etc., can solve the problems of reducing motor speed regulation performance, motor phase current distortion, and different debugging results, so as to solve the problems of low efficiency, low cost and convenient operation. Effect
- Summary
- Abstract
- Description
- Claims
- Application Information
AI Technical Summary
Problems solved by technology
Method used
Image
Examples
Embodiment Construction
[0029] The specific implementation manners of the present invention will be further described in detail below in conjunction with the accompanying drawings.
[0030] For the position angle of the motor rotor, three Hall rotor position sensors a, b and c installed on the motor stator are used to obtain the position angle, as shown in figure 1 As shown, but in practical applications, A, B, and C are the coordinate systems corresponding to the three-phase stator windings, and the assembly error of the Hall rotor position sensor during installation (there is no installation error for a single Hall rotor position sensor) will cause the motor There is an error between the actual position of the rotor and the position of the motor rotor detected by the Hall rotor position sensor, so we have designed a method for obtaining the position angle of the motor rotor that corrects for this error.
[0031] For three Hall rotor position sensors installed on the motor stator, such as figure 1 ...
PUM
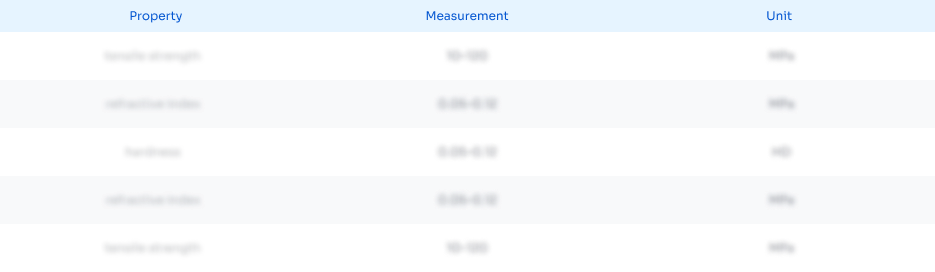
Abstract
Description
Claims
Application Information

- Generate Ideas
- Intellectual Property
- Life Sciences
- Materials
- Tech Scout
- Unparalleled Data Quality
- Higher Quality Content
- 60% Fewer Hallucinations
Browse by: Latest US Patents, China's latest patents, Technical Efficacy Thesaurus, Application Domain, Technology Topic, Popular Technical Reports.
© 2025 PatSnap. All rights reserved.Legal|Privacy policy|Modern Slavery Act Transparency Statement|Sitemap|About US| Contact US: help@patsnap.com