Null space bearing composite fault diagnosis method based on fault features
A technology of fault characteristics and composite faults, applied in the direction of mechanical bearing testing, etc., can solve problems such as rare application of mechanical fault diagnosis
- Summary
- Abstract
- Description
- Claims
- Application Information
AI Technical Summary
Problems solved by technology
Method used
Image
Examples
Embodiment Construction
[0032] The present invention will be described in further detail below in conjunction with the accompanying drawings and embodiments.
[0033] Such as Figure 1-5 As shown, a zero-space bearing compound fault diagnosis method based on fault characteristics, (1) establish a bearing fault vibration model according to the fault mechanism of the bearing. According to the structural characteristics and dynamics of the signal, it can be known that the vibration form of the rolling bearing fault can be approximately regarded as a mass-spring-damping system, and the dynamic model of the mass-spring-damping system is:
[0034] my″+cy’+ky=0
[0035] where m is the mass of the mass element in the mass-spring-damper system, c is the damping coefficient of the damper in the mass-spring-damper system, k is the elastic coefficient of the spring element in the mass-spring-damper system, and y is the mass in the system The displacement of the component is a function of time t, y′ is the firs...
PUM
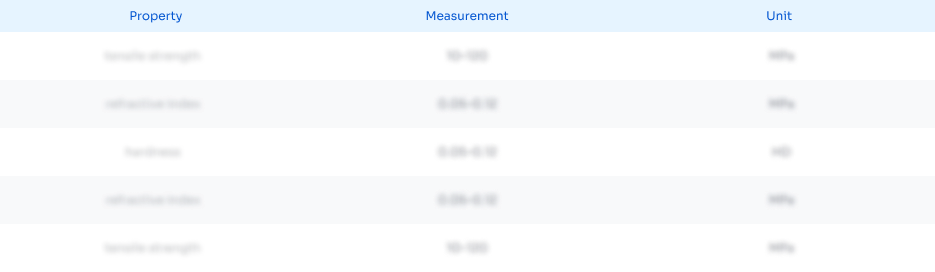
Abstract
Description
Claims
Application Information

- R&D
- Intellectual Property
- Life Sciences
- Materials
- Tech Scout
- Unparalleled Data Quality
- Higher Quality Content
- 60% Fewer Hallucinations
Browse by: Latest US Patents, China's latest patents, Technical Efficacy Thesaurus, Application Domain, Technology Topic, Popular Technical Reports.
© 2025 PatSnap. All rights reserved.Legal|Privacy policy|Modern Slavery Act Transparency Statement|Sitemap|About US| Contact US: help@patsnap.com