Method for optimizing internal structure of 3D (Three-Dimensional) printed object
An internal structure, 3D printing technology, applied in the improvement of process efficiency, instruments, energy efficiency and other directions, can solve the problems of the appearance of the model, save materials, eliminate stress, and maximize the physical strength to volume ratio.
- Summary
- Abstract
- Description
- Claims
- Application Information
AI Technical Summary
Problems solved by technology
Method used
Image
Examples
Embodiment Construction
[0047] The present invention will be further described below in conjunction with the accompanying drawings and embodiments.
[0048] Such as Figure 7 As shown, a 3D printing technology based on the Voronoi diagram and FEM to optimize the internal structure of the object, for an initially given solid model S, different sets of external forces F, here we assume that the model can withstand such a solid state External force, that is, there will be no area where the stress is greater than the yield point inside the solid model; otherwise, the solid model cannot withstand such a large external force, and there is no need to solve the optimization.
[0049] Next, in the case of ensuring that the model can withstand the set of external forces F, optimize the volume W of the model S , the objective optimization function is
[0050] min α , β W S ( ...
PUM
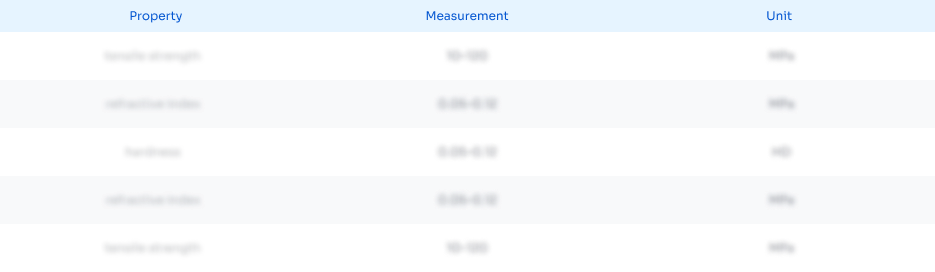
Abstract
Description
Claims
Application Information

- R&D
- Intellectual Property
- Life Sciences
- Materials
- Tech Scout
- Unparalleled Data Quality
- Higher Quality Content
- 60% Fewer Hallucinations
Browse by: Latest US Patents, China's latest patents, Technical Efficacy Thesaurus, Application Domain, Technology Topic, Popular Technical Reports.
© 2025 PatSnap. All rights reserved.Legal|Privacy policy|Modern Slavery Act Transparency Statement|Sitemap|About US| Contact US: help@patsnap.com