Container floor unit, underframe and method for producing container and underframe
A container bottom plate and production method technology, applied in the field of containers, can solve the problems of easily damaged floors, potential safety hazards, large welding volume, etc., and achieve the effects of high moment of inertia and bending section coefficient, reduced labor costs, and simple production methods
- Summary
- Abstract
- Description
- Claims
- Application Information
AI Technical Summary
Problems solved by technology
Method used
Image
Examples
Embodiment Construction
[0041] In order to further illustrate the principle and structure of the present invention, preferred embodiments of the present invention will now be described in detail with reference to the accompanying drawings.
[0042] In the present invention, when describing the orientation, the length direction of the container is taken as the longitudinal direction, and the width direction of the container is taken as the transverse direction.
[0043] refer to figure 1, the container underframe 1 includes: an underframe main body 10 , a gooseneck portion and a fork groove 13 . The underframe main body 10 is spliced by three integrated container floor units 11. In other embodiments, the three container floor units 11 of the underframe main body 10 can also be changed into a whole piece, or changed into Two or more container floor units 11 are spliced. The gooseneck part includes: a gooseneck groove 12 and two container floor units 11 respectively connected to the lateral sides of...
PUM
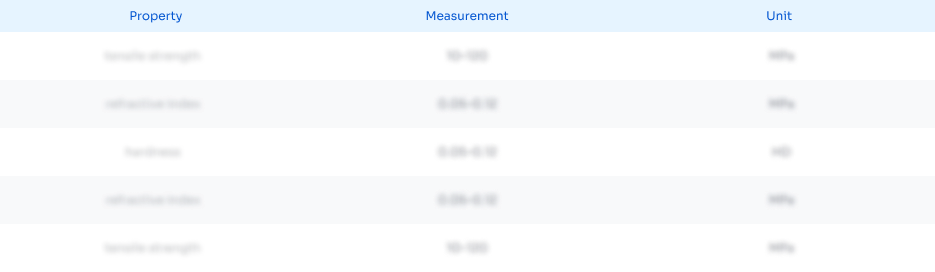
Abstract
Description
Claims
Application Information

- R&D
- Intellectual Property
- Life Sciences
- Materials
- Tech Scout
- Unparalleled Data Quality
- Higher Quality Content
- 60% Fewer Hallucinations
Browse by: Latest US Patents, China's latest patents, Technical Efficacy Thesaurus, Application Domain, Technology Topic, Popular Technical Reports.
© 2025 PatSnap. All rights reserved.Legal|Privacy policy|Modern Slavery Act Transparency Statement|Sitemap|About US| Contact US: help@patsnap.com