Application of aliphatic acid salt solution as rubber page rolling release agent and rubber page rolling method
A technology of fatty acid salt and release agent, applied in the direction of coating, can solve the problems of immature process, uneven application, high price, etc., and achieve the effect of easy process improvement, good isolation effect and low production cost.
- Summary
- Abstract
- Description
- Claims
- Application Information
AI Technical Summary
Problems solved by technology
Method used
Examples
Embodiment Construction
[0016] A rubber rolling method includes rolling and winding, the film after rolling is conveyed and immersed in a fatty acid salt solution, and then rolled.
[0017] The stearate may be stearate or palmitate, or a mixture thereof. There is no special requirement for the type of fatty acid salt.
[0018] As a further improvement of the present invention, in the above production method, the temperature of the fatty acid salt solution does not exceed 80°C, more preferably, the temperature of the fatty acid salt solution is 30-70°C.
[0019] As a further improvement of the present invention, in the above production method, the fatty acid salt solution is an aqueous solution of fatty acid salt.
[0020] As a further improvement of the present invention, in the above production method, in the fatty acid salt solution, the mass percentage concentration of the fatty acid salt is not less than 10%.
[0021] As a further improvement of the present invention, in the above production me...
PUM
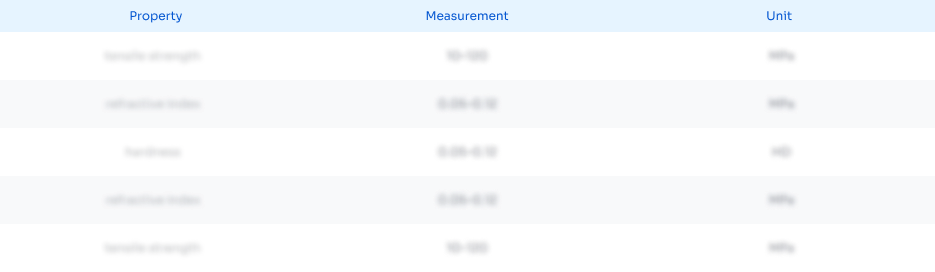
Abstract
Description
Claims
Application Information

- R&D Engineer
- R&D Manager
- IP Professional
- Industry Leading Data Capabilities
- Powerful AI technology
- Patent DNA Extraction
Browse by: Latest US Patents, China's latest patents, Technical Efficacy Thesaurus, Application Domain, Technology Topic, Popular Technical Reports.
© 2024 PatSnap. All rights reserved.Legal|Privacy policy|Modern Slavery Act Transparency Statement|Sitemap|About US| Contact US: help@patsnap.com