A green preparation process of phenolic resin without waste water discharge
A phenolic resin and preparation process technology, applied in the field of green phenolic resin preparation process, can solve the problems of high concentration of reaction products, severe reaction heat release, overflow of the kettle, etc., and achieve the effect of easy large-scale batch production, simple process and stable reaction
- Summary
- Abstract
- Description
- Claims
- Application Information
AI Technical Summary
Problems solved by technology
Method used
Examples
Embodiment 1
[0016] This example is a green preparation process of phenolic resin without waste water discharge. First, molten phenol is added to the reactor, and then the temperature is raised to 50°C. Then, the screw pump is used to divide the paraformaldehyde and the catalyst into the reactor for 4 times on average. In the reactor, the paraformaldehyde and the catalyst are added within 4 hours. After the addition of the paraformaldehyde and the catalyst, continue to keep warm at 75 ° C until the material reaches the expected viscosity, and then cool down and discharge the material to obtain a phenolic resin product.
[0017] Wherein the molar ratio of paraformaldehyde and phenol is 0.5:2.0; the molar ratio of catalyst and phenol is 0.1%; wherein the catalyst is sodium hydroxide.
Embodiment 2
[0019] This example is a green preparation process of phenolic resin without waste water discharge. First, molten phenol is added to the reactor, and then the temperature is raised to 70°C. Then, the screw pump is used to divide 5 times and the paraformaldehyde and catalyst are fed into the reactor on average. In the reactor, the paraformaldehyde and the catalyst are added within 5 hours. After the paraformaldehyde and the catalyst are added, continue to keep warm at 80°C until the material reaches the expected viscosity, and then cool down and discharge the material to obtain a phenolic resin product.
[0020] Wherein the molar ratio of paraformaldehyde and phenol is 1.0:1.0; the molar ratio of catalyst and phenol is 0.3%. Wherein the catalyst is potassium hydroxide.
Embodiment 3
[0022] This example is a green preparation process of phenolic resin without waste water discharge. First, molten phenol is added to the reactor, and then the temperature is raised to 90°C. Then, the screw pump is used to divide 6 times and the paraformaldehyde and catalyst are fed into the reactor on average. In the reactor, the paraformaldehyde and the catalyst are added within 3 hours. After the paraformaldehyde and the catalyst are added, the heat preservation is continued at 85° C. until the material reaches the expected viscosity, and then the temperature is lowered and the material is discharged to obtain a phenolic resin product.
[0023] Wherein the molar ratio of paraformaldehyde and phenol is 2.0:0.5; the molar ratio of catalyst and phenol is 0.5%. Wherein the catalyst is a mixture of ammonia and sodium carbonate.
PUM
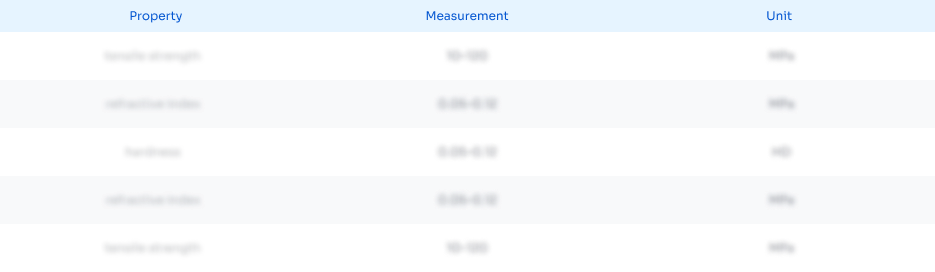
Abstract
Description
Claims
Application Information

- Generate Ideas
- Intellectual Property
- Life Sciences
- Materials
- Tech Scout
- Unparalleled Data Quality
- Higher Quality Content
- 60% Fewer Hallucinations
Browse by: Latest US Patents, China's latest patents, Technical Efficacy Thesaurus, Application Domain, Technology Topic, Popular Technical Reports.
© 2025 PatSnap. All rights reserved.Legal|Privacy policy|Modern Slavery Act Transparency Statement|Sitemap|About US| Contact US: help@patsnap.com