A method for improving the flexibility of polypeptide film by using polypropylene glycol and polytrimethylene carbonate
A technology of methyl carbonate and polypropylene glycol, which is applied in the field of polymer film preparation, can solve the problems of rigidity of the polypeptide and lack of flexibility of the polypeptide film, and achieve the effects of improved flexibility, easy mastery, and simple operation
- Summary
- Abstract
- Description
- Claims
- Application Information
AI Technical Summary
Problems solved by technology
Method used
Examples
Embodiment 1
[0014] 1) Synthesis of polypeptide-polypropylene glycol graft copolymer:
[0015] Add 12 grams of poly(γ-benzyl-L-glutamate) with a molecular weight of 60,000, 3.1 grams of polypropylene glycol monobutyl ether with a molecular weight of 1000, and 0.9 grams of p-toluenesulfonic acid into the dry reactor, and then add 260 ml 1,1,2-Trichloroethane solvent, under an inert atmosphere, stirred and reacted at 55°C for 2 days, terminated the reaction, and then obtained the target product by filtration, dialysis, and drying;
[0016] 2) Preparation of Polypropylene Glycol and Polytrimethylene Carbonate Modified Polypeptide Film:
[0017] Add 10 grams of polypeptide-polypropylene glycol graft copolymer and 38.2 milliliters of 1,1,2-trichloroethane solvent in the drying reactor, and add polytrimethylene carbonate (polytrimethylene carbonate) accounting for 2% of the total weight of the modified membrane in addition. The molecular weight is 4000), under an inert atmosphere, stirred and m...
Embodiment 2
[0020] 1) Synthesis of polypeptide-polypropylene glycol graft copolymer:
[0021] Add 12 grams of poly(γ-ethyl-L-glutamate) with a molecular weight of 70,000, 5.3 grams of polypropylene glycol monobutyl ether with a molecular weight of 1500, and 0.91 grams of p-toluenesulfonic acid in the dry reactor, and then add 216 milliliters of 1 , 1,2-trichloroethane solvent, under an inert atmosphere, stirred and reacted at 56 ° C for 3 days, terminated the reaction, and then obtained the target product by filtration, dialysis, and drying;
[0022] 2) Preparation of Polypropylene Glycol and Polytrimethylene Carbonate Modified Polypeptide Film:
[0023] Add 10 grams of polypeptide-polypropylene glycol graft copolymer and 36.5 milliliters of 1,1,2-trichloroethane solvent in the dry reactor, add the polytrimethylene carbonate ( The molecular weight is 5000), under an inert atmosphere, stirred and mixed at 47°C for 50 minutes, formed a film by casting method, and dried in a vacuum oven at ...
Embodiment 3
[0026] 1) Synthesis of polypeptide-polypropylene glycol graft copolymer:
[0027] Add 12 grams of poly(γ-methyl-L-glutamate) with a molecular weight of 80,000, 7.2 grams of polypropylene glycol monobutyl ether with a molecular weight of 2000, and 1.03 grams of p-toluenesulfonic acid in the dry reactor, and then add 177 milliliters of 1 , 2-dichloroethane, under an inert atmosphere, stirred and reacted at 57 ° C for 3 days, terminated the reaction, and then obtained the target product by filtration, dialysis, and drying;
[0028] 2) Preparation of Polypropylene Glycol and Polytrimethylene Carbonate Modified Polypeptide Film:
[0029] Add 10 grams of polypeptide-polypropylene glycol graft copolymer and 35.8 milliliters of 1,2-dichloroethane into the drying reactor, and add polytrimethylene carbonate (molecular weight 6000) accounting for 4% of the total weight of the modified membrane ), under an inert atmosphere, stirred and mixed at 50°C for 60 minutes, formed a film by casti...
PUM
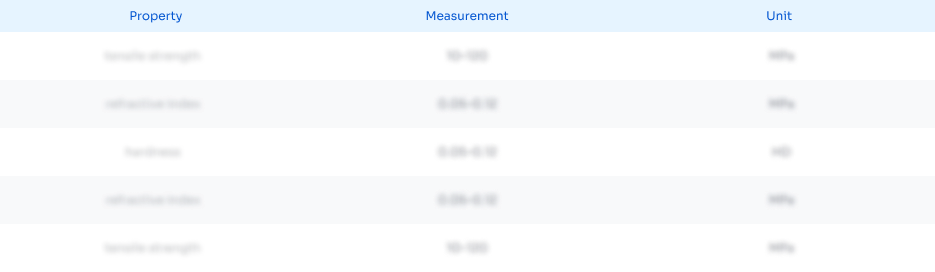
Abstract
Description
Claims
Application Information

- R&D
- Intellectual Property
- Life Sciences
- Materials
- Tech Scout
- Unparalleled Data Quality
- Higher Quality Content
- 60% Fewer Hallucinations
Browse by: Latest US Patents, China's latest patents, Technical Efficacy Thesaurus, Application Domain, Technology Topic, Popular Technical Reports.
© 2025 PatSnap. All rights reserved.Legal|Privacy policy|Modern Slavery Act Transparency Statement|Sitemap|About US| Contact US: help@patsnap.com