Automatic circular processing method of negative plate in subsequent electrolytic zinc electrolysis section, and implementation device
A technology of automatic circulation and processing device, applied in the direction of electrolysis process, electrolysis components, photography process, etc., can solve the problems of large labor volume and long cathode plate processing time, and achieve the goal of reducing labor volume, realizing clean production and shortening processing time. Effect
- Summary
- Abstract
- Description
- Claims
- Application Information
AI Technical Summary
Problems solved by technology
Method used
Image
Examples
Embodiment 1
[0039]The size of the cathode plate is 600mm×800mm. Use the manipulator to lift the cathode plate from the electrolytic tank and move it to the loading rack; high-frequency beating: transfer the cathode plate from the feeding rack to the beating device, and use the beating device to beat the electrolytic zinc electrodeposition area on the upper end of the cathode plate, Make a certain gap between the electrodeposited metal zinc sheet and the cathode plate; pre-stripping: After beating, transfer the cathode plate to the knife device for pre-stripping, and the knife device will shovel down vertically from the gap generated on the cathode plate. After a small drop of 20mm, separate from both sides of the vertical cathode plate, and then lift to separate from the cathode plate; peeling: then transfer the cathode plate to the knife device for complete peeling, the knife device fits the cathode plate, and vertically along the gap between the cathode plate and the metal zinc Shovel d...
Embodiment 2
[0041] The size of the cathode plate is 650mm×750mm. Use the manipulator to lift the cathode plate from the electrolytic tank and move it to the loading rack; high-frequency beating: transfer the cathode plate from the feeding rack to the beating device, and use the beating device to beat the electrolytic zinc electrodeposition area on the upper end of the cathode plate, Make a certain gap between the electrodeposited metal zinc sheet and the cathode plate; pre-stripping: After beating, transfer the cathode plate to the knife device for pre-stripping, and the knife device will shovel down vertically from the gap generated on the cathode plate. After a small drop of 25mm, separate from both sides of the vertical cathode plate, and then lift to separate from the cathode plate; peeling: then transfer the cathode plate to the large knife device for complete peeling, the large knife device fits the cathode plate, and vertically along the gap between the cathode plate and the metal z...
Embodiment 3
[0043] The size of the cathode plate is 550mm×600mm. Use the manipulator to lift the cathode plate from the electrolytic tank and move it to the loading rack; high-frequency beating: transfer the cathode plate from the feeding rack to the beating device, and use the beating device to beat the electrolytic zinc electrodeposition area on the upper end of the cathode plate, Make a certain gap between the electrodeposited metal zinc sheet and the cathode plate; pre-stripping: After beating, transfer the cathode plate to the knife device for pre-stripping, and the knife device will shovel down vertically from the gap generated on the cathode plate. After a small drop of 30mm, separate from both sides of the vertical cathode plate, and then lift to separate from the cathode plate; peeling: then transfer the cathode plate to the large knife device for complete peeling, the large knife device fits the cathode plate, and vertically along the gap between the cathode plate and the metal z...
PUM
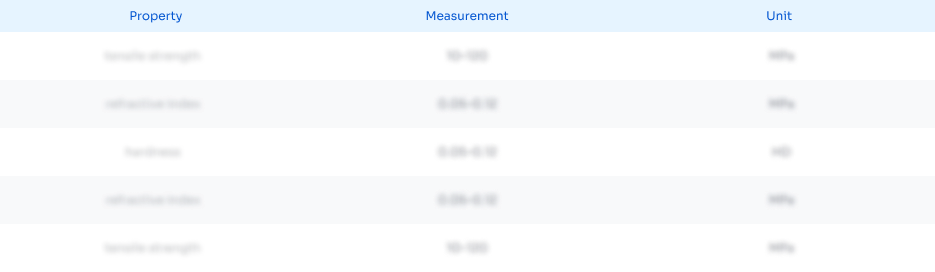
Abstract
Description
Claims
Application Information

- Generate Ideas
- Intellectual Property
- Life Sciences
- Materials
- Tech Scout
- Unparalleled Data Quality
- Higher Quality Content
- 60% Fewer Hallucinations
Browse by: Latest US Patents, China's latest patents, Technical Efficacy Thesaurus, Application Domain, Technology Topic, Popular Technical Reports.
© 2025 PatSnap. All rights reserved.Legal|Privacy policy|Modern Slavery Act Transparency Statement|Sitemap|About US| Contact US: help@patsnap.com